Computer technology has made a significant impact on machine tools and changes the areas of manufacturing and machining. When CNC technology was conceived, it was meant only for specific machines like machining centers and lathes were fitted with computer control. Today, however, CNC has made it into the world of highly productive and highly flexible equipment. Aside from these machines, new design concepts for machines facilitated the incorporation of different types of machining processes into a single machine.
This new technique has become possible mainly because of the computers that control most of today’s CNC machines. Thirty years ago, the biggest challenge was to exhaust the limited abilities of the machines. Nowadays, the biggest challenge is the ability to program, set-up, and operate the machines to produce highly precise CNC machined parts.
The success in producing CNC machined parts is not only dependent on the capacity of CNC machines but also on the professional development and training of their staff in equipping them with CNC skills. New skills like organizational preparation and planning, groundbreaking job processing methods, and the ability to manage complicated machine tools.
At present, many experienced machinists can run CNC machines to produce complicated and precise CNC machined parts. When considering cost and machining, here are some of the issues that you need to consider.
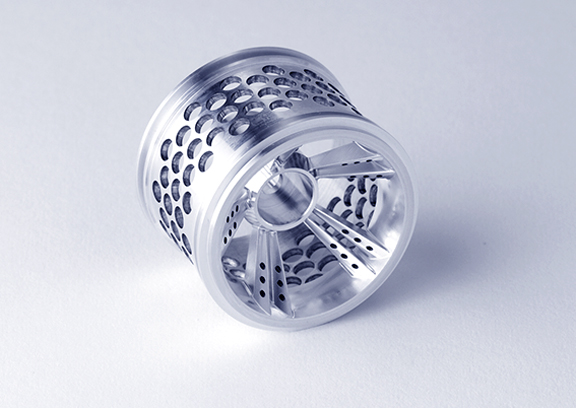
cnc machined parts*
Avoiding Redesigning the Machined Part
In manufacturing CNC machined parts, the problem usually lies not in the process but the preparation. The common issue is when the design engineer and the machinist are not on the same page. When the machinist receives the drawing, they study the part that they are going to produce. First is they will determine if this part is possible to make and then what machine they are going to use to make the part. Not everything in the paper can be produced in the machine. Therefore, engineers must be aware of its limitations before they make the design. It is a must that their vision is in line with the capabilities of the CNC machines and what the vendor has.
Additional Steps May be Needed
The most common challenge in producing CNC machined parts is deburring one with very small components. One example is a part that is as small as a pencil head on the design, but, it is as tiny as a pinhead in scale and specs. Such a small component is challenging to make and needs an additional secondary process to complete in high-precision.
There are stumbling blocks that appear when you are not expecting them. Sometimes, it happens when the part is on the final stage of production when the machinist found out that a secondary process is required for the necessary threading. It could have been more cost effective if the part is completed in a single process.
Some Simple Features May Require Complex Process
This issue is an exception as it can occur somewhere during the process itself. An example is in producing a part of a cathode ray tube. The process involves machining two separate metal tube into a solid center plate. It may seem simple, but the project requires removing 98% of the mass and drilling a small burr-free hole in the center to join the cavities. The configurations of these holes are complicated and challenging because you must make sure that the center is exact and of the correct size. But this is not the trickiest part yet. Instead, it is on making sure that we don’t break any tools and wear out the boring bars.
Material Matters
In CNC machining, choosing the material is a critical consideration. In the drawing board, it may look like an excellent machined part to make, but upon closer examination, the engineer will find out that the material it requires is hard to machine well. Certain materials cannot withstand the process. The designer must consider this too.
A classic example of a material that will have an issue when using CNC machining is tungsten. It is challenging to finish the part in the exact way that the customer wants it because it is more likely that parts made of tungsten should be ground and not machined.
Communication is the Key in Manufacturing CNC Machined Parts
According to expert machinists and practitioner of CNC machining, the most issue that needs to be resolved is communication. On top of the expertise of the design engineers, the machinist, and the accuracy of the provided drawings, the relationship between the engineers is the most important. It enables the manufacturer to recommend the best machining process to come up with a high-quality and precise CNC machined part.
Communication between the machinist and the engineers play an essential role in achieving the desired outcome based on the specification, on the budget and its schedule.
Reference
*Image from on https://www.arvindesign.info