3D printing technology is not exactly new in the world of manufacturing. The procedure has been around for some time now, but it wasn’t until recently that the oil and gas industries have taken an interest on everything related to it. As it happens, most energy-related markets could get some real benefits by embracing rapid prototyping as well as additive manufacturing to improve their performance and development.
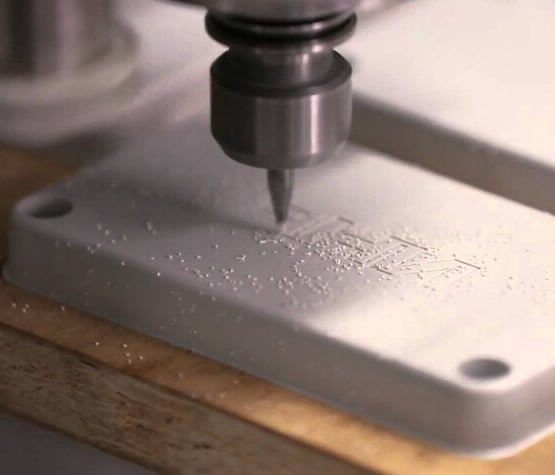
rapid prototyping services*
The costs of working with overseas manufacturing, as well as rapid prototyping, keeps getting lowered every day because of the fast rate at which new technology is developed in this field and how every new device drives the overall cost of equipment down. There are more diverse 3D printable materials than ever, and as a result, 3D printing and rapid prototyping are becoming readily available to the mainstream consumer market.
It’s also pretty helpful the fact that the expiration time of patents related to manufacturing is pretty quick. This makes these 3D printing technologies available to the world, and more people can dip their toes, in making this tech more reliable and functional. Rapid prototyping allows us to manufacture parts by following intricate plans that translate to complex shapes and smaller sizes. The procedure also reduces waste and lowers the costs of the materials used to create a product.
The Benefits of Using Rapid Prototyping in the Oil and Gas Industries
There are two takes on this, the upstream and the downstream. We will talk first about the upstream. In this stance, the main advantage is the shortened supply chain on all operations. The whole process of manufacturing gets incredibly streamlined: we get to reduce delivery time, we get cost-reduction downtime, we get on-demand parts and on-site production of components. It also helps to print parts that we might not have in production anymore, thus improving the profits of upstream assets. It also grants significant advantages to capital projects by reducing the time of tooling and all the development process.
The downstream take is that there will be more streams of revenue our company will have the opportunity of disrupting a market if we are set on making that happen. When it comes to oil and gas companies, both have the need to supply chemicals and plastic resins used on 3D printers to optimize their business prospects. The full adoption of the rapid prototyping technology will only increase over the next decade, making 3D printing materials and powders available at retail. The more companies have a chance to evolve their business model to traditional outlets, the more their chances of becoming the kings of their niche.
Exploring Rapid Prototyping Technology
Many oil and gas companies have been working with 3D printing and rapid prototyping technology for less than five years. This seems like an exceedingly short time given the benefits they can get out of it. The hard truth is that it will take a while for most companies to catch up and replace most of the metal they have been using for quite a while now. The current test ground for many of these companies is their direct clients such as Airlines and motorized vehicles which have embraced the tech quicker and high rates of effectiveness. Most of them take notice of how plastic parts handle their products. Plastics, after all, don’t create the levels of friction that metal can manage, and many of these resins have proven to be pretty durable when facing fuels at high temperatures.
By using rapid prototyping technology, these companies can leverage their capabilities to manufacture parts with even more complex geometric structures at very low costs. Certain components, such as combustion gas turbines can be redesigned using a CAD model to introduce an innovate shape and geometry that will help it reduce emissions while improving its performance. These big companies now can venture on more substantial spaces and plan new designs with an extended reach of possibilities to make lasting changes. The only thing needed are engineers with the right mindset and a transformative approach.
Closing Thoughts
Just imagine making obsolete the system bolted parts, getting rid of braze and welding. We could have components or pieces printed in a single piece to simplify the manufacturing and assembly processes. The time it will save to our company, and our clients could be the big break of whoever figures out this tech in favor of the industry. There is a long way to go, but we can certainly start on the right path by making a thought-provoking call on the use of the 3D printing technology at our disposal, as well as the freedom we offer to our engineering teams to tamper with known procedures and improve them to make them better or at least more functional.
Reference
*Image from on https://www.rapidprototypechina.com