It happens to the best in the business, and it’s not so uncommon. Before we get started, we need to make something clear: you have to get your mind out of the gutter because we are talking about shrinkage of plastics here. Every single manufacturer in the business has dealt with this issue before. They get commissioned to do a project, and the client is bent on using specific polymers that don’t suit their project to keep costs low. You unsurprisingly expect the result, but it still causes the outrage of the project manager: the parts are uneven and shrunk, and they don’t work at all that way.
Shrinkage is one of the most common problems in plastic injection molding procedures. It affects every single type of polymer regardless of the quality and the experience of the manufacturer. Even if they have the expertise to understand why certain options work better than others in some projects, their advice falls on deaf ears because their clients are used to have their product delivered in a certain way. They want to keep their quality standards even if you offer a better alternative. Brands working with silicone products are the ones facing these issues more frequently than other niches.
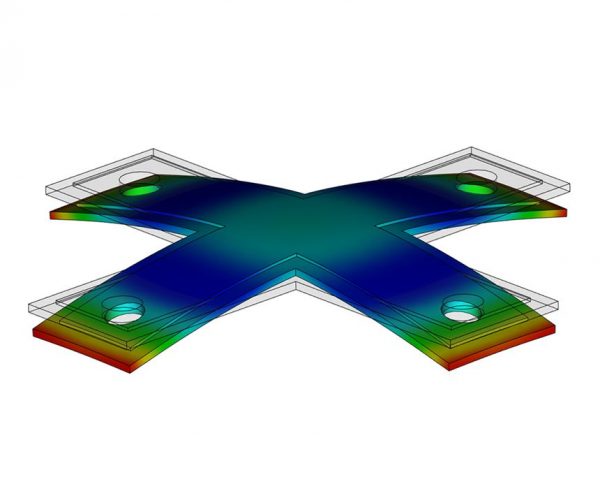
Shrinkage variation of an injection molded parts*
While we make it sound like a big deal, shrinkage is one of those issues that can be quickly dealt with by any competent manufacturer. Most of them take it for granted and can account for it with their longstanding clients that keep ordering their products from their workshops. The most common way to solve this problem is by increasing the size of the cavity mold by 1% or as big as 4%. It all depends on the material as well as the data regarding the shrink rate of it. Shrinkage happens when the product gets a chance to cool off after being released from the mold. It takes about 24 hours to get a full look at the actual effects of it on the product.
The Downsides of Shrinkage on Plastic Injection Molding Projects
With shrinking rates as high as 4%, the best way to deal with this problem is by thinking ahead of it. A proper manufacturer accounts for it based on past experiences and builds the shrink on the mold before starting the production cycle. Wall thickness also shrinks at different rates, and we also need to deal with sinking on these products. Sink is something that affects ‘products with uneven surfaces that have thicker areas. Engineering and design have to crunch some numbers to make this work the right way. Otherwise, you will be facing other issues such as:
· Sink Marks in Thin Plastics
We have stated that shrinkage happens as the part cools off. This process takes longer if the part has thicker areas. The rate of shrinkage is higher in those areas of the part, and they can deform the piece causing deep sink marks. Professional manufacturers know how to deal with this situation way ahead. Most of them work unorthodox methods, while others go for classic fixes using customized technology.
· Silicone Shrinkage
Silicone is probably one of the most flexible plastics out there, and it shrinks at the same rate even if the piece is thicker in some areas. This makes this material much more predictable to work with. It’s also preferred by many for a lot of products. The main issue with silicone is under-cured parts in a product that can deform the piece.
· Post Baking
This issue happens to some plastics that take a long time to get curated after cooling off. It affects a lot of the softer polymers out there since they can remain soft on the inside for a long time and become under-cured. The worst part of it is that it can slip by the eyes of the manufacturer if he’s not looking out for this particular issue.
· Full Deformities
Deformities are the bread and butter of plastic injection molding is the manufacturer is not working with the proper specs for a given project. It usually happens as the product is being removed from the mold, or if it’s being curated inside of it. This usually signals that we are not handling something in the manufacturing process the way it’s supposed to be.
· Backrind
It is a problem that happens if we increase the curating time of a piece inside the mold instead of letting it post bake properly. The plastic will expand under the pressure created by the heat, and it will press on the sides of the mold and divide the parting line. This is essentially the worst-case scenario because it creates a hell of a mess on the plastic injection molding machine.
You can deal with these problems if you hunt down for a great manufacturer that understands the properties of every resin you need for your project. Remember that cheaper options lead to inexperience most of the time!
Reference
*Image from https://www.ptonline.com/