The term high-speed machining evocates the process of making a mold for most people. The technology, however, is continually being used by most CNC workshops to optimize their workload. As incredible as it sounds, this CNC machining method has a vast range of applications that are used all over the place in most tasks. The groundwork that cemented the basic perceptions of most people about this machining method comes from the fact that high-speed machining was indeed introduced in the die-cast molding industry, and it was slowly incorporated in the machining technology. These days high-speed machining is a term of reference used for tasks that require the extraction of large pieces of material in a sheet. This is often used to increase the output and shorten the production cycle.
The Cost of Setting Up High-Speed CNC Machining
Using new technology probably sounds easy, but high-speed CNC machining can be incredibly challenging. It all begins with the design phase that determines the overall complexity of the part being created. If the product has an easy design, you can expect a delivery rate increased as high as 70% of the time you would wait using traditional machining methods. Even complicated stages such as pocketing are easy to handle with high-speed machining. Most CAD/CAM programs run the current versions of the software using high-speed machining algorithms. The combined efforts of the programs and the hardware can help you create brand new paths to the tooling efforts require to use your CNC machines at the top of their game.
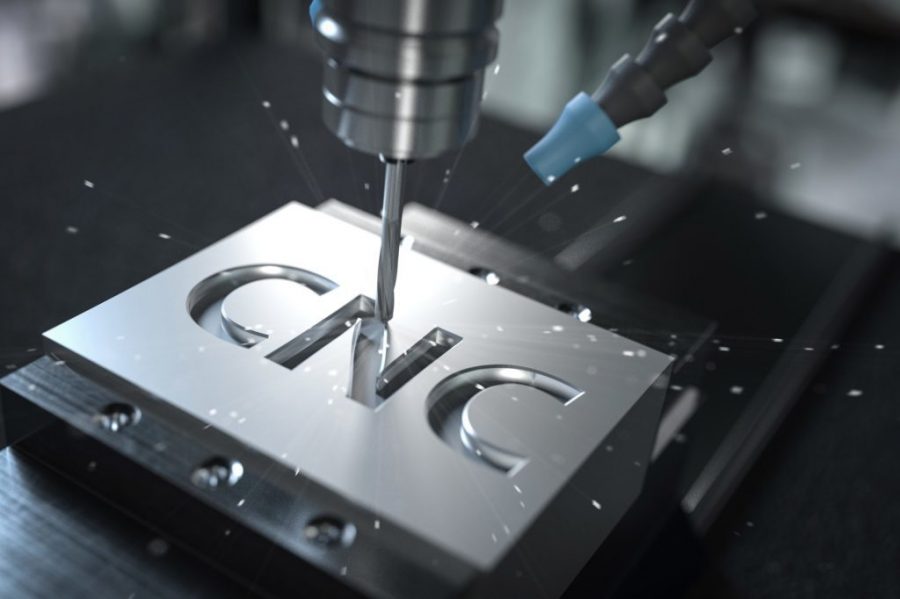
CNC spindle*
Faster Machining, Faster Output
High-speed CNC machining is mostly associated with spindles that run as fast as 15,000 rpm. The figure is a sight to behold, and it’s something the human eye can barely manage to catch. The greatest secret, however, is not a faster spindle by itself. The whole piece of hardware demands adjustments to be able to comply with such feats. Newer models are built to handle high-speed CNC machining. They are lined with thermal compensators, increased machine rigidity, sturdier builds, revamped positional feedbacks, modern control systems, tighter tool holders, and many more features that make it easy for them to handle this type of tasks. As we mentioned previously, older models can be adapted, but all the modifications and fixes can’t compare with a brand new piece of equipment.
The Old Ways of CNC Machining
In the recent past, hard materials were treated using electrical discharge machining. This process proved to be incredibly useful, but it had an incredible handicap: the expenditure of energy was too much. Using this process was not cost-effective at all. The manufacturing industry has been built on innovation. This forward-thinking led to the evolution of these machining methods into something incredibly productive and not as expensive. As CAD/CAM programs evolved, so did the hardware that worked with it. Mold casts were the first ones to reap the benefits of high-speed machining. The tooling for a mold suddenly was something easy to do, and the turnaround time decreased from months to days. CNC developers sought to optimize other stages of machining with the same methods that had made molding cast so productive and profitable.
Leaping Forward in the Manufacturing Industry
This ongoing and silent evolution led us to the devices we have today. The hardware that handles high-speed CNC machining has a different built than other devices of the same class. They are noticeable robust, and they carry a lot more tools to do what they are supposed to. These machines create cutter paths with consistent chipping and near-perfect tool engagement. They can handle the corners of the most complex parts with ease. Their range of motion is vast, and although the tolls move at inhuman speeds, the rest of the robotics handles the task with swift precision. These devices have finite control since they rely heavily on automated processes. They control the amount of material they can handle at a time, and the programming of cutting parameters is almost infinite if we have the imagination and the patience for it.
Looking Forward to the Future of High-Speed CNC Machining
The contrast of the work created with high-speed CNC machining is overwhelming when compared with the traditional tooling of older devices. Older CNC machines create their tool paths using racetrack patterns that follow the overall shape of the piece created by the machine. The older method lacks the amount of control offered by the new technology. Precision is an issue when compared with the older methods, to the extent of being awkwardly visible in some cases. The new ways indeed demand a lot more input from the technician, but as it happens when you drive stick, you also have full control over your project. Forget about heat-ups, friction, and all the other issues brought by traditional machining. High-speed CNC machining is here to stay.
Reference
*Image from https://www.superiorspindle.com/