Vacuum casting is a process that uses vacuum to draw in the liquid material in the mold. You use this process when air entrapment is a significant concern with the pattern. Apply this casting if the pattern involves intricate details and undercuts. Also, the process is applied if the material used in making the mold is a reinforced wire or fiber.
Thermoforming is the other term used to this type of casting because the process includes fast prototyping where it uses preheating of the plastic sheets. An automated casting machine is used in preheating the materials until they become pliable and soft.
Reason for Choosing the Vacuum Casting Process
The process produces high-quality products injection molded components. Casted models or testing and marketing objectives cast models. The final product has an impressive finishing that has drawn in a lot of people. No other technique can match the type of finishing this casting can do.
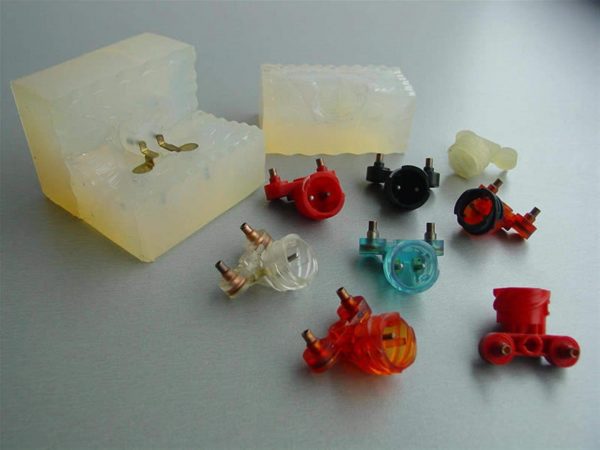
vacuum casting technologies*
Where to Use this Process
Used in testing a product before distributing it in the market.
Use the process for fast delivery production
It used in building models and prototypes.
Used for producing affordable low volume production
Used in developing a prototype of any size
How Does the Process Works
High-Quality Master Model
If you use the vacuum casting process, you need a high-quality master model. Also, you can use a model designed using stereolithography. Make sure that the model used is of the right dimensions and appearances. So, no flaws are transferred to the model after completing the process.
The Curing Process
Position the model into a two-part silicone rubber mold. The mold is then subjected to a high temperature to make sure the two parts will stick well. The curing process strengthens the pattern and making it more durable.
Cut open the cured mold to expose the hollow part at the center, which has the same size as the master model. Place the pattern into the vacuum chamber. Then the material is added into the mold to produce the product.
Filling the Resin
Fill the mold using the assigned material. The resin will copy the characteristics of the industrial material. Metallic powder or coloring pigment is then added to the resin materials to achieve the functional properties or appeal.
The mold filled with resin material is then placed inside the vacuum chamber to make sure there will be no air bubbles in the pattern. This will make sure that the final product is not damaged or ruined.
The Final Curing Process
Place the mold in the oven for the final curing. The mold is subjected to a very high temperature to make sure that the material is durable and robust. The silicone mold is then removed from the molding tool and used in creating more prototypes.
The final step in vacuum casting after removing the prototype from the mold is painting and decorating it. The designs and paintings are used to make sure that the product has an appealing look.
Reference
*Image from https://www.ineo.es/