For those who want to reproduce prototype designs quickly, vacuum casting is the perfect solution for you. The entire procedure is a fast, affordable, and accurate method for creating identical prototypes, especially in small quantities, making the process ideal for small businesses and start-ups.
Vacuum casting is typically a multi-step process that’s cost-effective, saving you both money and time in the long run compared to other reproduction techniques such as CNC machining. The tooling process uses a silicone mold, prototype, or a master model that can produce up to 50 identical machined parts/products.
At Lt Century, our prototyping and CNC experts will come up with a master model in-house incorporating all your ideas and design, thus reducing your overhead cost as well as significantly reducing the lead-time, which ensured your product hits the market faster giving you an edge over your competitors.
Vacuum casting is turning out to one of the essential procedures as the silicone molds can be used in producing parts of a wide variety of polymers with a large percentage of them that can be combined or layered to enhance their appearance as well as durability.
Vacuum casting presents a perfect solution for the production of multiple copies of prototypes at a lower cost and fast manner.
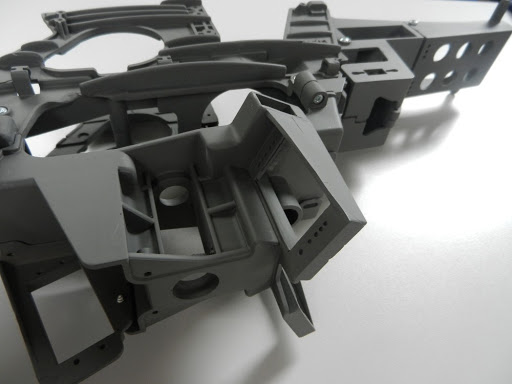
vacuum casting and assembled components*
The Three Main Stages of Vacuum Casting
Master Model Creation
A master model is an original design, prototype, or parts that are to be replicated. The model can either be produced on-site or submitted by the client; for submitted models, they have to be made using stable materials that can withstand curing temperatures of more than 40° C (104° F).
For clients who opt for in-house master models, our teams will be able to curate the master according to your specifications in a quick manner.
Mold Production
Using the master, the next procedure is the creation of a low-cost silicone rubber mold. Silicone rubber mold doesn’t require post-processing or extensive tooling before usage, unlike metal molds.
The silicone molds are produced quickly and can last longer, giving them the ability to be able to reproduce approximately 1-50 units before a replacement can be done. The silicone molds can be produced just within a few days, unlike when it’s done through conventional tooling, which significantly reduces your production time.
Prototype/Part Replication
The created mold is, in turn, filled using a wide variety of polymers that have been heated and cured; air particles in the mold are removed through vacuuming, which expands the polymers into each part of the mold cavity which ensures the finished product is identical just like the master model.
This stage also allows for the addition of a broad spectrum of colors and polymers with different ranges of opacity, giving you the designed freedom to produce parts or products using vacuum casting mold.
Vacuum casting presents you with the perfect solution for:
- Rapid production of silicone molds
- Reproduction of prototypes and parts at low-cost
- Testing features and concepts before large-scale production
Reference
*Image from http://mata3d.com/