The die casting process is one of the most in-demand manufacturing techniques nowadays. This comes as no surprise since there are many advantages to using this method.
This process involves a metal casting process that uses a mold cavity in combination with high pressure creates the designed part or product. These molds are machined from alloys with characteristically high strength, much like injection molding.
Die casting uses metals made from non-ferrous ones like copper, zinc, magnesium, aluminum, tin, lead, and many other alloys.
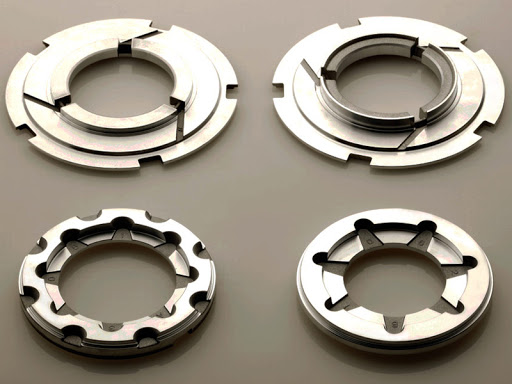
Aluminum die casting molds*
The Pros and Cons of Die Casting
Die casting is used in many industries including in the automotive, industrial, lighting, household, and medical industry. Here are the advantages and disadvantages of die casting.
Advantages of Die Casting
High Efficiency
The die casting process has a simple mechanism and is automated. Thus, it has a higher output that is a good thing, especially when the product demands high volume manufacturing.
Excellent Accuracy and Smooth Surfaces
Die casting has a high tolerance and even higher precision. Because of its high dimensional accuracy and high surface finish, you can expect the product to be of high quality. The product can be used directly, with less machining, and improves the utilization of the alloy. It also saves machining costs.
High Mechanical Properties
The melted metal in die casting cools quickly and it can crystallize under pressure. This layer of crystalline grains on the surface of the die casting is usually compact and fine. It contributes to the strength and hardness of the product.
Complex Thin-Walled Parts
The die casting process produces complex walls that are thin-walled, thinner than the ones produced by metal mold castings and sand castings.
Embedded Materials
In die casting, you can integrate the complex inserts and fasteners in the final product. This saves the materials cost and the cost of processing the part. It can even produce the most complicated shapes and the functionality of this part can be improved.
Easy for Mass Production
Because die casting can produce dimensionally stable and durable die-cast parts, there is no need for machining and in some less machining is required.
Different Surface Textures
The parts produced from die casting can have many finishing surfaces and techniques. This process also makes textured or smooth surfaces.
Disadvantages of Die Casting
Porosity
The porosity of the die casting part makes it hard for heat treatment. Aside from its porosity, the product is also made with quick filling and high pressure.
High Upfront Cost
The upfront cost in die casting is high because the mold can be expensive. However, with high-volume production, it can offset this cost.
Short Diecast Life
Die casting has a high melting point alloy and at some point, this causes thermal fatigue on the molds. As such, it can shorten the life of the molds.
Reference
*Image from http://www.diecastingschina.com/