Vacuum casting has truly revolutionized the way industrial prototypes and parts are created, the casting process provides manufacturers and clients with an effective and fast way of producing high-grade and quality parts and products.
Before full-production commences, the casted parts can be first produced in small quantities which enables both designers and engineers to test the functionality and design of the parts or products and allows for alterations in case the client’s specifications are not met.
The whole casting process uses re-usable casting resins and silicone molds which provides similar copies as the master model. The parts and components from the master have a wide variety of uses such as testing, product development, marketing, and crowdfunding campaigns just to mention a few.
For this post, we are going to briefly discuss what the whole process entails and why you should seriously consider this production technique into your product development.
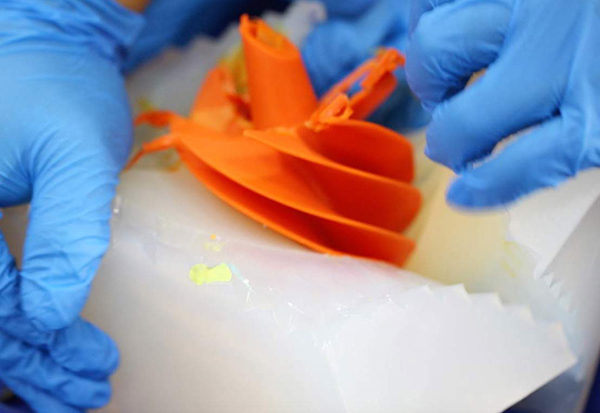
Vacuum casting products*
The vacuum casting process
The process initially begins with the creation of the master, in simple terms the master is the is a prototype created from durable and robust materials.
When it comes to the creation of the master model, two key machining services are mostly used: CNC machining services and 3D printing as they are swift and flexible thus can accommodate changes during the casting process.
During master model preparation, you must pay special attention when it comes to sanding and polishing surfaces. Once all the patterns are now ready, they are placed onto the casting box which is then wholly filled with liquid silicone.
The next process is the curing phase, this usually happens in the oven till everything solidifies and it, in turn, ejected out. The solid mold is cut by following delicately following the seam line and the pattern is removed thus creating a hollow cavity that mirrors the original master model.
Production will only begin after the mold is completely sealed; a feeding tube is inserted into the mold which leads to the cavity.
The next step is filling the cavity with liquid urethane resin and then it’s moved into the vacuum chamber; the resultant vacuum removed all the air bubbles from the chamber thus allowing the liquid resin to fill the entire chamber.
Reasons why vacuum casting is preferred compared to prototyping
Vacuum casting is slowly emerging as one of the go-to manufacturing techniques as it comes with a myriad of benefits such as:
Final products are of great quality: The master patter is created to perfection; with vacuum casting, you’ll expect nothing short of quality. The identical copies are a replica of the master.
It’s fast: In comparison to prototyping methods which primarily uses steel, the silicone molds are fast and simple to produce and takes just a few days. This is the best scenario when you are working on a tight deadline.
Comes with great versatility: Even though there is a wide variety of ways of building prototypes, only vacuum casting can create products that look, feel, and appear like the master. Additionally, you can use a wide variety of materials such as polyethylene, nylon, and ABS just to mention a few.
Reference
*Image from https://www.ddprototype.com/