In the manufacturing world, every industry relies on sheet metal manufacturing one way or the other. Name an industry, from appliances, automotive, electronics, to energy, and you will find that there is a use of sheet metals. Everywhere you look, you will realize that sheet metal is part of huge amounts of everyday products.
When it comes to sheet metal manufacturing, there are lots to talk about. However, for this article, we will go back to the basics. Why? Because it is also necessary to know this manufacturing process well to find out if it fits our manufacturing requirements.
Here is an in-depth look at sheet metal manufacturing, the process, materials, and what we can benefit from using it.
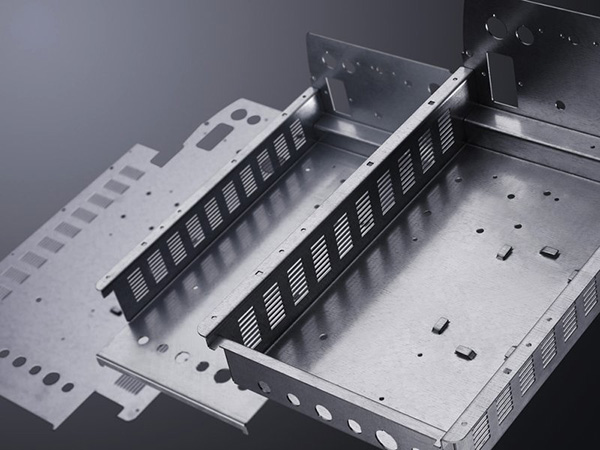
Sheet metal bending*
The Manufacturing Process
It is easy to define sheet metal fabrication. It starts with a piece of sheet metal, and then it is shaped into the desired part by simply forming or deforming and through material removal. The sheet metal, which is the workpiece in this process, is a common raw material. The thickness that can be used for fabrication is not specific, but it can range between 0.006 to 0.25 inches. This thickness is often indicated as gauge and is between 3 to 39.
What does the number in gauge mean? Generally, the higher the gauge, the thinner is the sheet metal, and its exact dimensions will depend on the material.
As we said, sheet metal can be bent, cut, and stretch into any desired shape. It can also undergo material removal processes when there is a need to create holes and cutouts, which are two-dimensional shapes. Sheet metals can be bent at different angles multiple times, or it can be stretched to form complex contours. Examples of a metal part produced from this process include small brackets or washers, enclosure for appliances, and large airplane wings. Thus, you can find sheet metal manufacturing as an integral part of many industries.
Sheet metal fabrication is classified into two kinds: cutting and forming. Rolling machines used to form steel into round parts is an example of forming categories, while cutting torches used to break large chunks of sheet metal into pieces is cutting.
One of the most common processes in metal fabrication is welding. Through this method, various pieces of metal parts are formed together to create the desired results. When the fabrication is done, additional finishing processes like powder coating, painting, and plating is applied.
Advantages of Sheet Metal
Sheet metals provide a host of benefits to every industry. Because it has a low weight to thickness ratio, it is easy to transport and work with. This material is also durable and strong, which makes it ideal for a variety of applications. Its malleability is also an asset because it can be bent, cut, and formed into any shape. This quality allows fabricators to provide clients with highly specialized solutions and customized designs to meet their requirements.
Another benefit of using sheet metal is its relatively low cost, which is ideal for one-off designs and also for large scale production. And lastly, this material is easy to repair, making it a practical choice for a variety of applications.
Reference
*Image from http://www.hand-packing.com/