It’s common knowledge that all parts and products used in the medical industry virtually start-out as prototypes. Prototypes are important in every manufacturing process as they provide proof-of-concept, certifications, engineering testing, design models as well as benchmarking just to mention a few.
For this sole reason, vacuum casting is the perfect rapid prototyping service used in high volume production. Injection molding needs a solid metal tool and for this reason, it’s advisable to create the first few prototypes using the vacuum casting technique. This will enable designers and engineers to perfect the specifications and designs before finally committing to an injection molding tool.
Prototypes created using the vacuum casting technique are of high-quality and can also be used for a wide range of engineering testing. So, let’s discuss some of the main advantages of using vacuum casting in created medical products and applications.
Fast and Reliability
First of all, it’s important worth noting that vacuum casting begins with a master pattern, the pattern is a replica of the final part to be produced. This is often made using 3D printing or CNC machining.
Once the master is ready, the mold can be produced in less than 2-3 days. One day is solely dedicated to the pouring of silicone while the other will be for curing. This process is faster compared to creating plastic injection molds from aluminum or steel.
Once the mold is finally ready, the resin is poured into the cavity thus creating the final product in one or two days. Taking into account the whole process, from concept to finished product; plus making the master pattern, all of it can be done in less than a week, and in some instances, it’s less than that.
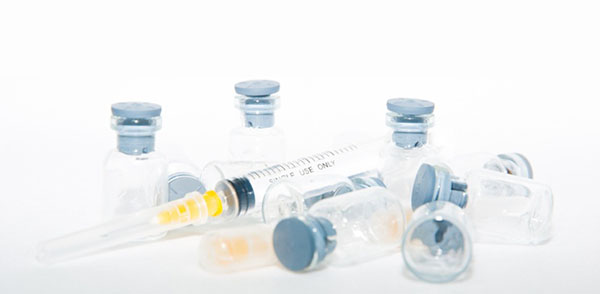
Vacuum casting products in medical applictaion*
The casted parts are of high-quality
The resin cast copies of the master have similar qualities and features compared to the master pattern. This includes texture, fine surface details, tolerance, and dimensions just to mention a few.
What this simply means is that the casted parts perform and look like the machined parts of plastic injection molded products and parts. Another vital thing is that they can also be post-machined like other solid parts and products.
Its smooth surface texture makes it simple to apply finishing services without the need for extra polishing or sanding.
Availability of a wide range of plastics
Parts and products used in the medical sector must show a wide range of mechanical and chemical properties. They have to be sterilized, easily cleaned, transparent, biocompatible, chemical and heat resistant, rigid, and strong amongst other things.
To meet all these requirements, the casted resins can meet all the qualities and so much more. This fact Is quite beneficial when floating a new medical design for approval by the FDA.
Affordable
It’s always advisable that you monitor and control every cost associated with every step of production. Creating a master pattern using vacuum casting and making resin copies as well as silicone molds requires little investment.
In most production cases they are quite affordable compared to CNC machining or 3D printing.
Reference
*Image from https://www.craftechind.com/