Rapid prototyping is a crucial element in the engineering of automobile parts these days. It brings a lot of positives to the assembly details of most motorized vehicles in the market. There is also plenty of advantages that brings affordability and quick turnout to many parts.
Many companies’ ongoing rising standards can be met without issues, and profits have gone on the rise on par with new and improved safety measures in place. The overall take is that rapid prototyping is good for business.
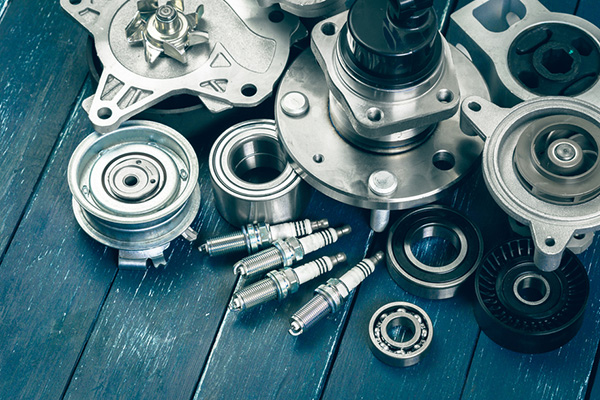
Auto parts*
Here are some of the most significant contributions this manufacturing technique has to offer to the auto parts industry:
Upholstery and Control Console
Most vehicles come equipped with a great set of control and indicators in their central console and control panel. Since many brands are focusing more on customizing their cars to their clients’ demands, rapid prototyping proves to help get these newly minted ideas done in no time.
Custom Made Exterior Builds
Many people tend to believe that the main bodywork of the card is composed of one single piece. Such is not the case. Most of what you see can be altered and customized to cover the specifics of vehicle users, such as those modified for disabilities or those spiked up by owners who are not entirely happy with the original design.
Engine Parts Using Aluminum Machining
Design mockups and functional versions of automotive engine parts are becoming cheaper, thanks to rapid prototyping. The use of aluminum has been widespread because it is lightweight, has high heat transfer, and low cost.
Lighting Parts Using Acrylic Machining
Acrylic is a type of clear resin that can withstand the elements while retaining its transparency. Its easy machinability and durability add to its physical properties that make it perfect for automotive lighting. Rapid prototyping can bring out the best of this material while keeping the quality at a low cost.
Part Prototypes Using Injection Molding and Rapid Tooling
Automotive parts typically have intricate designs. A few reasons are comfortability for interiors, aerodynamic stability for exteriors, and safety for functional details. A quick way to make batches enough for the supply chain is using injection molding and rapid tooling.
Vehicle manufacturers create around 13,500 cars every day. But constant development requires them to have unique parts. That is why creating a few functional auto part prototypes is necessary, leaving no choice for designers other than rapid prototyping.
Reference
*Image from https://www.repricerexpress.com/