1. High-Quality
Vacuum casting is a viable option for prototyping because of several factors, the most important of which is the high quality it produces. Although vacuum casting is most often used for prototypes, it may lead to increased efficiency, even competing with injection molded parts. Vacuum casting is ideal for the manufacturing of microscopic, high-resolution components because the mechanism can perhaps create the finest features on a master model. It’s important to remember, though, that the final product can only be as good as its master model. Keep in mind that the master model produced either from a CNC machine or a 3D printer should have a smooth surface and crisp details for the best results.
2. Material Selection
If you require a wide variety of materials for your rapid prototypes, vacuum casting is an excellent solution. While silicone is typically used for mold making, a wide variety of polymer resins (such as rigid polymers, flexible epoxies, transparent materials, and more) can be used for the final casting. For example, polyurethanes that look and act like ABS are one type of moldable and curable resin, whereas polyurethanes that mimic PE/PP are another. That’s right, your vacuum molded model can look and function just like the finished, mass-produced components you’ll be using ABS or Polyethylene (PE) for, to name a couple.
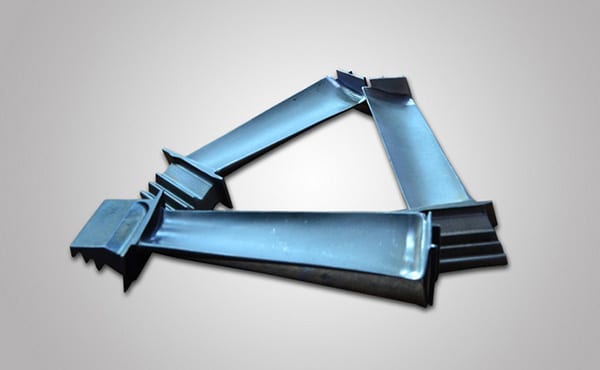
vacuum casting gas turbine parts*
3. Testing Phase
It has been demonstrated that accurate prototypes may be made via vacuum casting from a variety of materials. This translates to fit testing if the part of a bigger assembly and operational validation and testing for vacuum cast prototypes. This feature is useful because it allows manufacturers to test their products for quality and viability in specific contexts before committing to full production. Therefore, pre-series production using vacuum casting is an advantageous rapid prototyping procedure for mechanical and esthetic validation, certifications, and client trials.
4. Time Required
Vacuum casting can be an efficient method for producing plastic prototypes. In addition to helping you save time, vacuum casting is also a useful tool for speeding up the creation of new products. Metals like steel are used for tooling in more traditional molding methods like injection molding. These are well suited for production runs, but their lengthy development time makes them inappropriate for prototypes. However, a silicone mold can be made in less than a day, and several cast pieces can be made quickly and in succession with only a single mold. When time is of the essence, and you need to show a prototype to stakeholders or get into market tests, vacuum casting can help you get there faster.
5. Cost
Finally, vacuum casting is a cheap method of making high-quality prototypes or pre-series items in small batches.
It’s because of a couple of things: Firstly, the low cost of energy consumption is a result of the fact that vacuum casting uses far less energy than injection molding or CNC machining.
Second, once the reference model is made, most of the expense of vacuum casting is incurred through the resin chosen. The effort needed to cast components using this approach is less complex than machining. Besides this, silicone molds are cheap (even less than aluminum or steel molds).
Reference
*Image from https://www.tradeboss.com/