Milling is reasonable for some, various highlights, including stringing, chamfering, opening, and so on. This takes into consideration creating complex plans on a solitary CNC processing focus with lucky exactness. The resistances are around +/ – 0.1 mm.
The production of these previously mentioned highlights requires a wide range of processing tasks such as surface milling and face milling along with angular milling and form milling followed by profile milling, gear milling, and so on.
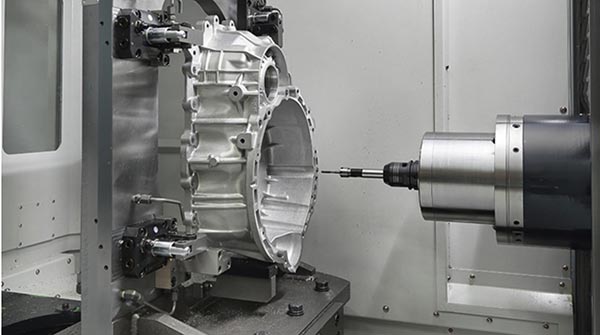
CNC mill lathes*
Plain milling: Plain milling is additionally usually known as surface milling. It utilizes a flat plant, which means the cutting device’s rotational hub corresponds to the cutting surface. Surface milling can use various cutters, full or restricted, contingent upon the vital result. Utilizing a full shaper can bring about quick material evacuation when combined with moderate cutting velocity, fast feed rate, and coarse teeth of the shaper. The surface completion of such cutting may not meet the prerequisites.
Along these lines, a subsequent advance can incorporate a difference in devices to utilize better teeth. Likewise, this requires quicker cutting velocities and more slow feed rates, so the measure of material expulsion per time unit is more deliberate. Simultaneously, the last completion is progressively precise. Along these lines, the mix of the two settles on for a decent decision from a financial point of view.
Face milling: This activity utilizes a cutting apparatus with teeth on the sides just as in the end. The instrument’s pivot is opposite to the machined part. Face milling frequently comes after surface milling, as it can create progressively mind-boggling shapes and leaves a pleasant completion. The teeth on the sides do most of the cutting work while the teeth on the tip deal with the surface completion.
Angular milling:This milling activity lets us make chamfers, grooves, and so forth. There are a few different ways to achieve these highlights.
If there should be an occurrence of a normal 3-pivot factory, the utilization of various cutters bodes well. These can be dovetail cutters to create calculated notches or only a factory with a funnel shaped cutting head for chamfering. Note that these two are fundamentally the contrary energies of one another. The pivot of the shaper can be opposite or in accordance with the surface.
Form milling: This kind of milling requires unique tooling to make progressively complex surface forms. Curved and inward cutters are the two instances of the tooling that discover use here. Form milling assists with making these surface shapes in a solitary cut. The instruments can help make round breaks, round edges, and so forth. The apparatuses must have the correct boundaries to accomplish the ideal result. Group milling is a sub-class of the formmilling whereby using a few cutters without a moment’s delay can make designs.
Profile milling: A typical milling activity to create arched and inward parts. The procedure incorporates 3 stages – roughing, semi-completing and wrapping up. Roughing utilizes round additions to accomplish the underlying work for expelling the majority of the material. Ball-nose end factories are the ideal fit for semi-completing and wrapping up. Such work will generally profit by CNC milling, as 4 and 5-hub innovation can extensively animate the tasks just as give better quality.
Gear milling: Indeed, processing additionally discovers use for creating gears. The entire procedure of creating gears includes two stages. First comes gear milling. The material non-abrasiveness powers making the part without breaking a sweat while accomplishing extraordinary resilience. The apparatuses then experience a warmth treatment procedure to solidify the surface. From that point onward, CNC turning will be answerable for the ultimate result.
Bottom line
After settling on your decision, it is ideal to pick a dependable manufacturing contractual worker for the activity.
Reference
*Image from https://www.dwproducts.com/