Machine tools are an essential part of custom CNC machining. Picking the right tools make all manufacturing procedures possible. If we have an understanding of these parts, we can have the best custom machined projects done in a matter of moments. Think about any shape or structure. It doesn’t matter if we are talking 3D shapes or 5D, 1,5mm pieces or 250mm. With the right tools, there is nothing CNC machine tools can’t create. Think of it this way: CNC machines are the brains that will execute your project using the tools you have chosen for it.
CNC machines are still regarded as a new technology by many people around the world. Machine tools, however, have been around for a long time. Most of these tools predate CNC technology and the inclusion of computer machinery for at least three solid decades. Like the manufacturing procedures they are complementing today, these tools have evolved with. There is no need to manually handle these tools since a computer can do a much more efficient job. CNC machining can handle manufacturing tasks at a fraction of the time that a handcrafter used to make.
To get all the machined parts we need in the most diverse shapes, CNC machines use several types of CNC tools. The catalog of these tools is as vast as the number of materials that can be worked on CNC machines, most of them being able to handle with ease metals and polymers, while other can easily take on wood or anything that comes to your mind. The level of success on each project is defined by how much thought goes behind it. Most of these custom CNC machines have to be appropriately programmed to make sure they make proper use of the tools at their disposal.
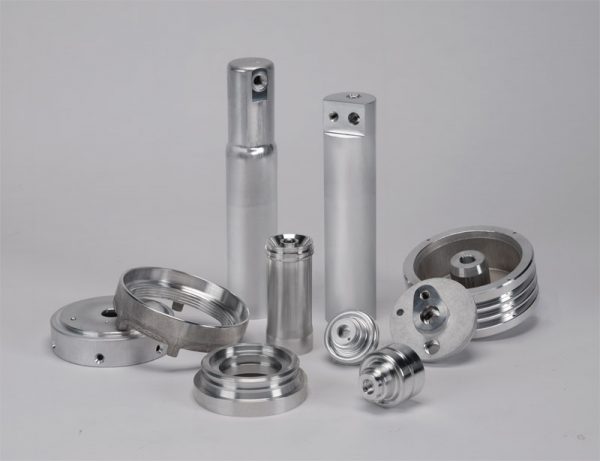
cnc machined parts*
The following is a list of the most popular machine parts to customize a CNC Machine
·Turning Centers
Turning centers are also known as lathe tools, and they are probably the most popular choice on the list. They are commonly used to create cylinder-shaped parts. Lathe tools are equipped with a tube-like piece that can hold the material that is being worked on while a cutting tool strips down the exceeding of it to mold it into the desired shape. The result is a cylindrical piece with parallel sides and circular ends.
Turning centers are often considered very versatile since they can create such a broad range of products. They can handle the most intricate designs easily with high levels of tolerances and exacting specifications. A lathe tool is divided into horizontal lathes and vertical lathes. The first one is used to create light to medium-weight pieces while the second one is used to deal with heavier crafts that can’t be draped on the work floor.
·Swiss-Style Turning
This is a lathe tool that is mostly used to work with components that can handle high-production tasks. The tool is fast and is regarded as the most reliable above all of the other ones mentioned in the list because of its durability. The tool can dish complex pieces in the millions with great attention to detail, more than anything offered by any turning tool available in the market. Swiss-style turning is the best option because it uses one of the most precise feeding techniques, using a rigid guide bushing to feed the materials to the machine and providing a firm base for faster speeds of performance. Given the extreme attention to detail offered by this lathe, it’s one of the favorites machines used for industries that rely on precision such as the medical and aerospace.
·Metrology Machines
This is an upgraded version of a quality checking machine. Metrology technology uses the latest 3D technology to get a further look and detect anomalies in the CNC machined parts. As expected, this is a lot of help for the manufacturer whose goal is to achieve higher accuracy levels and enhanced tolerances on their finished products without too much trouble. The increased levels of accuracy translate to less rejected parts, higher profits, and lower costs of production.
·Turn-Mill Centers
This tool is a two-for-one package that offers the best features found in CNC turning and milling. They are often regarded as very versatile tools since in it’s a pretty popular choice among manufacturers who don’t want to buy separate machine tools for turning and milling. The merging of operations in a single device opens the door to intricate machined parts that can be created in no time. Ultimately this device is considered a time-saver by insiders in the industry since it cuts down the setup and operation time and enhances the quality of the finished product.
·Shaper Tools
A sharper tool is very small in size, and it’s used to machine a straight tool path. With this tool, the cutter is placed on top of the fixed piece that is being tooled, and it gives it the freedom to move following a lined pattern.
·Bridge Mills & Gantry Machines
Bridge Mills and Gantry machines are regarded as highly functional pieces of equipment, but they are often used to create substantial frames on the structure of transportation vehicles in the automotive and aviation industries.
·5-Axis Machine
A 5-axis machine is a tool that can move in five different directions in one stretch to give us a product with high levels of accuracy at a fraction of the time it would take to create the same part using conventional means levels in record time. They don’t require a lot of setup time, even for the most complex projects.
Reference
*Image from on http://www.jlometal.com