Explained in Layman terms, die casting is a manufacturing process used to create metal parts by passing molten metal at high pressures inside steel molds that are known as dies. The dies are created using specialized tooling, and they trace a pattern that contains the liquid metal that produces the parts. After the molten metal goes inside the mold is left to cool and harden, to be removed later in a casting gate. Each piece is then trimmed down, and finishes are added if necessary.
Die cast parts are presented as something overly simplistic or really complicated, depending on the project. Die casting is also one of the many options currently available to create parts. The procedure must have something special since it’s still around even after plastic injection molding seems to be overtaking it at every turn. The hard facts are that metal is still very much in demand when it comes to manufacturing certain parts and products, and this not precisely going away any time soon. To illustrate the point, we present the advantages of die casting, and we compare it to other manufacturing procedures.
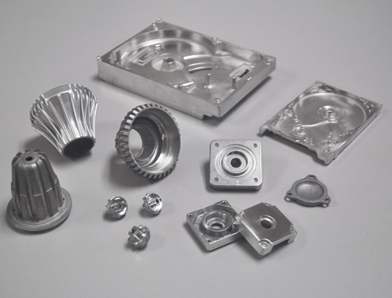
die casting parts*
First-Hand Benefits of Die Casting Metal
· It’s an efficient process
Creating the die is probably the most complex stage of manufacturing, and once you have it, you can create as many parts or products as you need, even in the thousands or millions, with minimal downside or defective products.
· It Works Consistently for Repeatable Parts
Die casting opens the doors to mass production as one of the best perks in ROI terms, but it also offers consistency. Die casting is a very precise manufacturing technique, and it has a high rate of consistency and repeatable results.
· It’s Customizable
If you need smooth or textured finishes in your parts, die cast metals can handle even the most intricate designs, so they look as you need them in accordance to your planned specs.
· It’s Flexible
On top of the customizing features, we already mentioned, you can work around certain issues with more precision such as the thickness of the part, and the complexity of it. Die cast parts can be as simple or as complex as you need them. Just make sure to work out all the detail in the design stage!
· It has a Long lifespan
Die cast parts are not weld or joined by sheer pressure. Most of these pieces are created using a single mold. This sole trait makes the products created with this technique stronger than any other parts created using other manufacturing methods. They are durable, as well as heat-resistant and dimensionally stable.
Getting a full overview of this list of benefits makes it easy to understand why die casting is still very popular, but this doesn’t mean that it’s the best manufacturing procedure for every single task out there. The creation of parts can be certainly achieved using many methods that work as well as die cast metal. This is how this procedure measures to some of them:
Die Casting Vs. Forging
Forging and die casting are very different manufacturing procedures. While die casting uses a mold and liquid metal to create a part, forging uses heat and pressure combined to create everything. With forging, we take a stock piece of metal and heat it to a temperature that allows us to mold it as we see fit. The pressure is applied by using a hammer or a mechanical press to shape them into what we need. Sometimes forging calls for a mold, but heat and pressure combined are used to get the metal inside it, rather than melting it. This manufacturing technique is for truly specialized jobs, and it’s often used for visual crafts rather than practical ones.
Die Casting vs. Sand Casting
A model is used to make an impression in a sand mold that is used later on to create metal parts. There is also an additional sand core that can be used to offer complementary shape to the interiors of the part, including holes and passages that are needed. The process is often perceived to be very similar to die casting, but the differences are more visible. Sand casting is an imperfect manufacturing process with a very low production rate because it needs time to create a single piece. Sand casting is another technique that is considered for craftier tasks instead of mass production.
Die Casting vs. Plastic Molding
Some would say that these two methods are rivals at odds since they work under the same principles. The only difference that can really tell them apart is the use of raw material to create the finished products with die casting using metals and plastic molding using resins. The only notable difference among them it’s how fast plastic molding can complete a production cycle, something that is compensated by die casting by offering better accuracy to the mold.
Reference
*Image from on https://www.jcyinternational.com