The injection molding process encompasses a lot of applications in manufacturing. This process is commonly used in creating items from toys, plastic trinkets, automotive body parts, water bottles, containers, cell phone cases, and a myriad of containers.
Generally, all the plastic products that we use every day are made from injection molding. It offers flexibility in size and shape which widens the design boundaries in creating products. The plastic material provides more design freedom and weighs less than any other material.
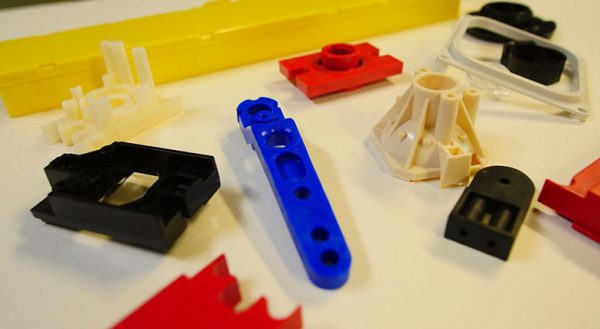
Plastic-molding-products*
How Does Injection Molding Works?
In the injection molding process, the injection machine has three major components: the heated barrel, screw, and feed hopper. The plastic in powder or granules is supplied into the hopper. Some of them are liquid forms like resins and don’t need heating.
When in solid form, the material needs to be melted through the frictional action of the screw equipped with heater bands. The molten material is then injected through the nozzle and to the mold cavity. It may sound easy but this process is a very complicated process in reality.
The material cools down while in the injection cavity and then it solidifies while taking the configuration of the cavity. When the part hardens, the platen that holds the mold will open and eject the product.
The Injection Molding Principle
The principle behind injection molding is straightforward. Yet, the practice of injection molding is not that simple at all. There are different consequences for heating plastics. They have complex behavior when melted and may influence processing complicated products.
Injection molding operates in pressure flow and heat transfer. It only needs the essential injection molding machine, which works on a press and a mold.
Advantages of Plastic Injection Molding
The injection molding process is a preferred method by many manufacturers because of its versatility in producing products and parts. Aside from this, it also has many advantages over other traditional manufacturing processes.
1. The automation process cuts manufacturing costs
Everything in injection molding is automated and the entire work is performed by robotics and machines with only one operator managing the production. This automation process helps reduce the cost of manufacturing since there is a reduction in overhead costs.
2. It allows for the use of many materials in one product
One of the advantages of using this manufacturing process is the use of multiple types of plastics at the same time. It has a co-injection nozzle that allows for flexibility in the materials used.
3. Finished products have enhanced strength
Injection molding uses fillers in the injection molds. The fillers have reduced the density of the material during the process but it also helps in adding more strength after the process.
4. It has high efficiency
The process is fast and one single mold can make hundreds if not thousands of parts. That translates to higher production output and that translates to lower cost and higher efficiency.
5. It allows for complex geometry and detailed features
The high pressure in the molding process makes it possible to add more details to the design of the product. It also means that intricate shapes and complex designs can be manufactured here.
Conclusion
Injection molding is a perfect choice as a manufacturing process for high volume production. There is also not much work required after its production.
Reference
*Image from https://www.amdekinc.com/