In the production process known as CNC machining, factory equipment and tools moved by pre-programmed computer software. From grinders and lathes to mills and routers, the procedure can utilise to operate various complicated machines. Lathes, routers, and milling machines with three, four, and five axes are typical CNC machines. They have CNC machining services that can produce end-use components in low volumes while enabling rapid prototyping. We assist you in choosing the best material and determining how to optimise the design. Nearly any stiff plastic and metal alloy can be precisely and consistently cut by CNC machines, making these parts ideal for every industry.
How Long Has CNC Machining Been Around?
Computer Numeric Control (CNC), is a technique that the society of Manufacturing Engineers has referred to as “marking the beginning of the second industrial revolution and the advent of an age in which the control of machines and industrial processes would pass from imprecise draught to exact science.” In the 1940s and 1950s, CNC machining services was a punched tape-based technology that quickly advanced to analogue and digital technologies in the 1960s. The inventor of CNC machining regarded as John T. Parsons. He created numerical control as the foundation upon which CNC machining built. The machining method, however, was created in 1751, long before Parsons.
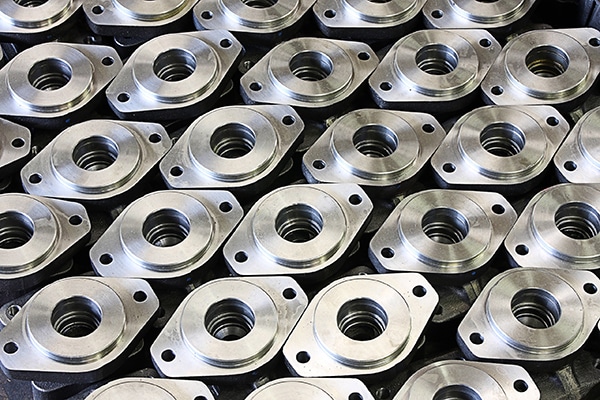
CNC machining parts*
CNC machine types
There a few things as you choose which CNC equipment to incorporate into your business. The two main categories of CNC machines are traditional technologies and cutting-edge machining technologies. There are benefits and drawbacks to each variety. Choosing type of CNC machine to add to workshop account the specific requirements of your project. Some of the similarities and contrasts between traditional and cutting-edge CNC machines covered in the following infographic:
Conventional Technologies:
Drills:
Drills operate by spinning a drill bit, moving it around, and coming into contact with a block of stock material that isn’t moving. Wherever you require precise holes, CNC drills can help.
Lathes:
Drills spin the block of material against the drill bit; lathes do the exact opposite (instead of turning the drill bit and putting it into contact with the material). Typically, a cutting tool is moved laterally on a lathe until it gradually contacts the material as it is rotating. Lathes are primarily employed with metals and wood, removing the surplus material to produce a lovely and yet more functional component.
Machines for milling:
The most prevalent CNC machine in use today is most likely a milling machine. Remove material from the stock unit, rotary cutting tools used. The skill carries out several tasks, including drilling, boring, cutting gears, and creating slots, a specific piece of material.
Benefits Of CNC Milling
Because machining techniques produce parts or components from a single workpiece, many firms favour them. There are various other benefits of CNC machining. Higher productivity CNC machining facilities can make parts around the clock. The machines might operate continually with minimal human involvement. A level of precision. Programming operations used in CNC machining are precise. These instructions followed by the machines without any unintended deviation or human error. The components will be identical, exact, and of excellent quality. Additionally, complicated, intricately designed items can produce using CNC machining.