CNC milling is probably one of the most rewarding tasks in the CNC machining industry. You get some of the most distinct products created with this technique, but it also takes a toll on the device doing the task since a lot of cutters get spent in the process. The secrets of managing your cutters better are in your accuracy with management and the quality of your hardware. We are going to discuss a few pointers to solve this problem and help you save some money.
Cutters are probably the most used part of milling tasks. They are the ones that are in contact with all the workpieces processed in our workshop. If your machine is not equipped with the right cutters for each job, the assignments will be mishandled, and you will lose a lot of money on spare parts. We are going to do a brief review of the reasons why cutters are damaged and how to avoid that issue by splitting the topic into the two stages mentioned: hardware and management.
Hardware Issues and How to Solve Them
The following is a list of the problems faced by any CNC milling machine when you are handling even the most basic task. Keep in mind that one or more of these causes can affect a project at any given state. Each problem is presented with a solution at the end.
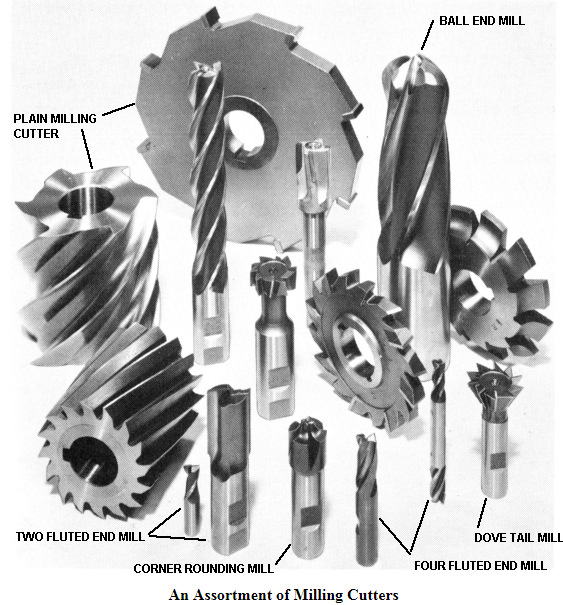
An Assortment of Milling Cutters*
· The Geometry of the Cutter is not the Right One
Each milling job is done by cutter, and each task will be done efficiently if you are using the proper equipment for the job. If you have doubts about the right cutter for a specific material, try one of wide diameter to get the geometric aspect of the piece done right. If you use a 1mm cutter against a workpiece with a thickness of 5mm, you will lose the blade in a matter of moments. A 2mm blade will do the job just fine without breaking. Increasing the number of flutes is also a solution, but it will increase the presence of chips on the surface. Working with short cutters is the best course of action for delicate materials.
· Blades Can Get Lost in a Runout
A runout happens in CNC milling machines when a cutting tool goes off-center on its rotation. This makes the spindle and the cutting blade to vibrate as it moves. The immediate consequence is that the machine will force itself to increase the cutting strength, which will stress the tool to the point of breaking it. To fix this problem, you will have to change the tool, and in a more severe stance, you will have to replace the spindle as well.
· You Don’t Know the Properties of the Material You are Handling
If you bring raw materials that you are unfamiliar with to your workshop, you are asking for a bag of problems that will have you covered in broken cutters real quick. Ironically these issues have the most straightforward solution and the one that is most commonly overlooked. Take a moment to research the material, ask other workshops on how they handle it, and always assume that the workpieces are harder than anything you imagine.
Management Issues and How to Solve Them
Management has to do a lot with geometry and angles. It may sound corny, but if you are working on any CNC milling machine, you need to hold the workpiece properly. You also need to be mindful of other aspects of the manufacturing process, such as you get the material on the CNC mill and getting the place of work clear of chips between products. We did the same as the previous take. We point out the problem alongside a solution for you.
· Holding the Workpiece the Right Way
If you are working with a heavy workpiece of raw material and it’s vibrating as you handle the task, something is not going right. This usually means that the cutter is not the right fit for the material. The most immediate consequence is the geometry of the product will get wonky, and the cutter will break. You need to set the proper feed and a labeled speed on the machine before each milling task. This is up to the engineering department in a workshop. If there is an ongoing problem in this regard, they are the ones who have to review the numbers again
· Starting the Milling Tasks at Zero Offsets
This stance falls on the operator of the CNC milling machine. They are the ones that have to place the sheets of material in the right position with the correct tooling following the specs of the delivered by the design department. The CNC milling machine should be homed before placing the material to avoid any issue or tool offset.
· Feeding the Material to the CNC Milling Machine
You can’t just take a workpiece and shove it on the CNC milling machine as you see fit. You need to start cutting accurately and avoid roughness if you are using small cutters. You can prevent any problem in this regard by turning the ramp entry at the lowest cut force possible. If you have to handle a straight down cut, make sure to set the lead-in speed appropriately to avoid any accident.
Clear the Chips on the Workpiece
There is no way around this one. Chips make everything difficult in milling tasks. Even the most sophisticated CC milling machine generates chips, and you need to clear them off the surface regularly to avoid damage to your finished part and the cutting blades as well. The only solution in this stance is to measure the timing and accumulation of chips and clear them with a blower or a vacuum when you need it.
Reference
*Image from https://www.metalcuttingvision.com