For companies looking for a cheap way to make a prototype, vacuum casting can be a great option. In this process, you need to have the exact temperature to cure the materials. The resin needs about 30 degrees to cut the shrinkage of materials from the vacuum pressure and the mold should be higher at 60 degrees.
While it is strict with its required temperature, the results are seamless. The finished product does not divert from the mold and it does not must further finish.
Want to know how your company can enjoy vacuum casting? Read this article to find out more.
The Vacuum Casting Process
Vacuum duplication or vacuum casting is the process that involves injecting the resin (material) into a mold made from silicon. It is a two-part process: creating the mold and injecting the material to create the finished part.
It is a low-volume manufacturing method, with a production output of ten to a hundred before discarding the mold. Vacuum casting is more suitable for pre-series production as it creates exact replicas of the model. The final product is most often used in visual and mechanical tests in product development.
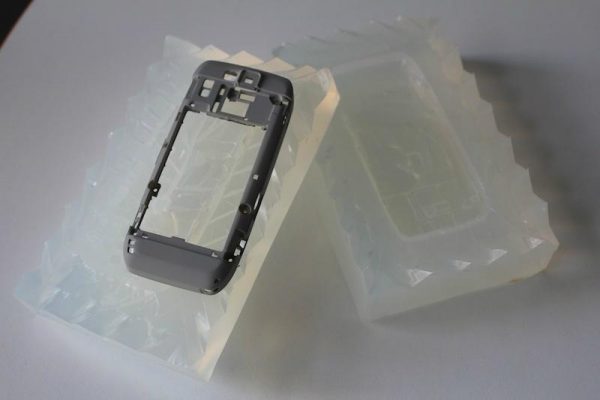
Vacuum casting*
Benefits From Vacuum Casting
The capability of vacuum casting in producing duplicate products has led to its many benefits. Here are some of them.
1. High Precision Finished Product
Since vacuum casting uses silicone on its mold, the final product is the exact copy of the model. It also ensures that the finished part acquires all the finer details of the model and ends up as a precise replica of the original product.
The mold is loyal to the details of the original even if it has complex geometries. The result from vacuum casting has also the qualities of the model.
2. High-Quality Parts
Since resin is used in creating the replicas, you can select the material that is as close to the one used in the original product as possible. You can select from the material with the right hardness, the correct rigidity and flexibility, and with the same appearance.
When coloring the material, it should be done en masse or it will have crystallized transparency. Vacuum casting also permits creating over moldings like brass inserts. It also allows for final products to have painted finishes.
3. Lower Cost and Shorter Turnaround Time
Compared to using steel or aluminum, using silicone is a lot cheaper in producing molds. Also, since you can make about ten to a hundred products out of one mold, it is more valuable than using 3D printing. And, since it needs about 7 to 10 days to complete the process to create about 50 prototypes, vacuum casting is the best choice when you are on a tight deadline.
Limitations of Using Vacuum Casting
Of course, vacuum casting is not without its limitations. First, is the limited life of the molds compared with injection mold. It also has a limited number of products that can be produced. But, since vacuum casting is geared towards low volume production, it can be justified.
Second is because vacuum casting requires the original model, it needs a little investment unlike in 3D printing. But because you can produce more than one product, you can distribute the investment to costs.
Conclusion
Vacuum casting is an economical option if you compare it with other prototyping methods. The finished products have lesser costs and the benefits outweigh its limitations.
Reference
*Image from https://www.diytrade.com/