When CNC machining is discussed in the broad spectrum, the topic of building a working supply chain for manufacturing is always popular for discussion. The management needs to build a seamless network of suppliers with vendors that will never let you down is not an easy task. It’s even said that those who have a better structure in their chains of supply are the ones who could easily overtake all other players in the market. The great news is that competition to have the best service in this field won’t stop anytime soon.
The most straightforward fact about this is that supply chains are not directly marketed the way they used to. In the old days, manufacturers could even their costs asking for large shipments. These days, the outlook of supply has changed with the number of options created by technology and sub-contracting services. Enterprise resource planning and material requirements planning go hand to hand to create parallel databases that, at some point, get merged to deliver a finished product in the market. Like a surgeon’s work, this needs precision, follow-up, and knowledge.
How can a buying team reduce management burden while maintaining a responsive and qualified fulfillment base?
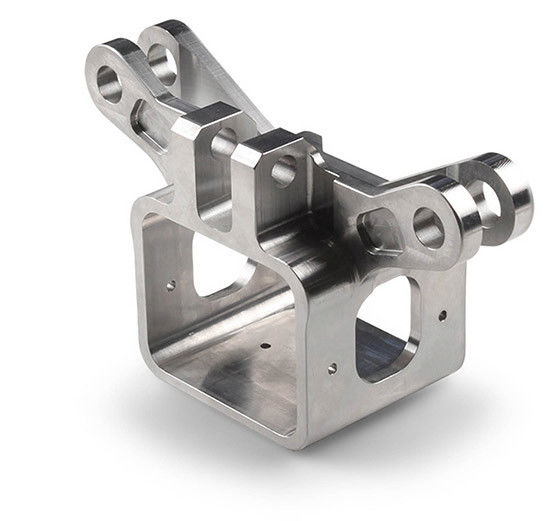
precision cnc machined parts*
Facts – A Larger Number of Suppliers is a Burden
A proper manufacturer is on the right track when he asks himself the right questions. Let’s get that out of the way for you at once because the challenge is straightforward: How can a supply manager make his life more comfortable with a system that is responsive and able to fulfill the needs of its clients? The trick is to cut out the fat of the process, but knowing which phase has to go is harder than it looks. Any workshop these days uses many suppliers, and each one of them works with a different set of paperwork because they hate to have their systems leaked, especially when they are successful.
There is more to this equation. Each vendor is prone to change the specifics of the deal they have with any manufacturer. They mostly do this based on the upgrade or downgrade of their capabilities. Since all of them have to comply with international regulations, they keep these ongoing changes in a fashion that turns into a logistical nightmare real quick. Vendors usually have their own tracking systems as well their customized scores to keep track of the performance of their personnel based on measurable metrics such as quality, on-time delivery, responsiveness, and more.
When a workshop has multiple suppliers, the task of doing a follow up with each one of them is strenuous, tiresome, and it takes a lot of time. Even with a Supply Manager on the job, this can get overly complicated if he doesn’t have a reliable system to keep track of everything he has to do. While it’s good to have a significant number of options to get your materials, managing the chain can bring a lot of problems on your end if the system it’s not optimized. In short: if you have to place many resources in your company to get what you need, your supply chain is broken.
Working With Fewer Suppliers – Not a Wise Move
The thing about the supply chain with any workshop is that less will never be better. No one has all the materials they need, and being picky about it will only diminish their manufacturing capabilities. This ongoing circle never seems to stop as many companies keep upgrading their operations with new services, and they get the machinery necessary to handle new projects. If the workshop doesn’t have options when it comes to vendors, they may face diminished revenues or overpaying to third parties to manage particular stages of a project for them.
If we move to logistics, that’s a whole different animal right there, since all vendors work at their own pace and following their own schedules. Most of them can do a great job scheduling, but they require a lead time and upfront payments to get started. Most of them offer quotes based on your state of urgency, and the cost of prioritizing you over everyone else can be pretty high. As you can guess by now, all these issues come from timing, and it’s so imprecise that there is no rulebook with a clear guide about how to solve it.
Navigating the Turbulences – How to Have a Flexible Supply Chain
Not all CNC machining jobs are the same. Nearly every single product created in a CNC workshop has its settings and specifications. We can’t escape the fact that we need multiple suppliers to keep a steady flow of business coming at our companies. One of the best solutions you can have to solve a portion of this issue is to join a network of vendors. There are many initiatives like this online, and it’s pretty easy to get in contact with them. By sharing some information about the capabilities of your workshop, you can trade materials, information, and other procedures to make sure you can fulfill your orders in time.
Reference
*Image from https://cymanufacturing.com/