One of the major steps of turning your dream into reality is knowing how much it costs to custom design your manufactured. When it comes to making sheet metal enclosures, panels or parts. There are a wide variety of options when it comes to making the final product according to your designs and specifications.
But when it comes to services, finished and materials used, there are bound to be the difference in pricing. For those who are budget-conscious, you will want to keep the below considerations to maximize all the cost efficiencies. In this post, we are going to discuss the tips that will enable you to keep your overall cost low.
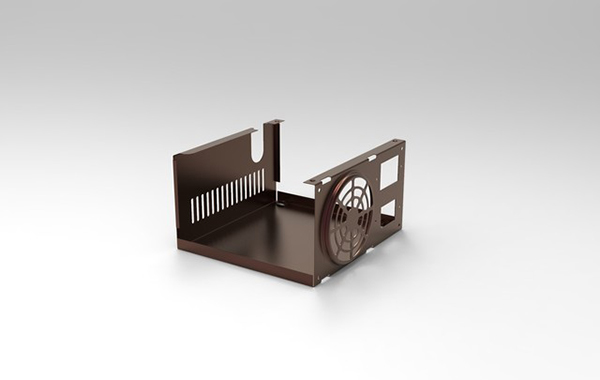
sheet meatal products*
1. Stick within the materials in stock
One of the most important tips for avoiding unnecessary costs is sticking with the stocked materials, components, and thickness. Its always recommended that you prepare an inventory list of all the hardware, components, fasteners, and materials that are in stock.
If you stick to what’s already in stock, then you can significantly reduce the cost and the extended lead times ensuring you make timely delivery to the market.
2. Stick to in-house
For clients, you should always choose firms or workshops that are one-stop-shop for everything. From graphics, chem film, brushing, powder coating just to mention a few everything should remain in-house.
But, in some cases, there might be a few finishing services that require third-party services such as tin plating and anodizing. For those looking to further cut costs, then you should consider in-house finishing services.
If anodizing and tin-plating is a must, then you should consider reaching out to a third service provider whose cost will fall in line with the budget range.
3. Choosing a cost-effective material
Aside from choosing a material that is already in stock, you should also choose a material that is cost-effective and falls within the budget range. One of the most economical materials used in sheet metal includes 5052 Aluminum or Cold Rolled Steel. On the higher side is stainless steel and copper.
4. Add counter-sinks but only if necessary
Countersinks are an important addition to any part or enclosure; this enables the fastener to sit flush on the metal surface. But if the design of your part and product have counterbores and countersinks throughout, then your project is termed as budget-sensitive and you might want to reconsider scaling it back.
This can be done by putting countersinks whenever possible.
5. Welding Vs Fasteners
With regards to attaching all the parts of your enclosure during assembly; you can either decide on two choices either welding them together or by use of fasteners. If you sticking within the budget, you can use fasteners in enclosures rather than welding. This is unless your project required welding, if not the latter is a perfect choice.
If your project requires welding, you can use the blend between the two that is spot welding and using fasteners to cut on cost.
Using sheet metal techniques that stick within the budget range is important as it will ensure the profitability of your business. Minimizing the input while maximizing the output should be your motto. Allows you to take full advantage of the die casting process.
Reference
*Image from https://www.cadcrowd.com/