Many industries use the process of vacuum casting to create duplicate materials or models of a particular object. Vacuum casting is mainly done on plastic materials at large. The various kinds of plastic materials that you see which are colorful and in different shapes and sizes or similar shapes and sizes, but of different colors for instant, pipes, mugs, glasses, etc. are the result of vacuum casting. Vacuum casting is also known as duplication. If you go to check online about vacuum casting, then you will get a very complex definition of vacuum casting including the words like resin, prototype, etc. which a man of common parlance cannot understand. So, today in this guide I will explain to you in simple very simple words what vacuum casting is and how the process is done to create a duplicate of a product or object, or material.
First Step to Vacuum Casting
The first step for vacuum casting is to use any object or master model or product of plastic i.e. is designed one (for instance a pipe or tiffin box or mugs), it is put into a rubber silicon casing, for getting its shape imprinted on the casing. Then, a vacuum is applied to the silicon mold (i.e. like a box shape) to remove any kind of air bubbles. Then, it is put in an oven-like heater for about 40 degrees Cl. Once it is cooled then the mold is cut and the master model is removed from the casing. After its removal, there is a perfect casting or replication of the master model that you get in the silicon casing. Then, the casing is closed and sealed. Then, the silicon mold casing is preheated in the oven at 70 degrees cl. After that, it becomes ready to be placed in the bottom of the vacuum casting machine.
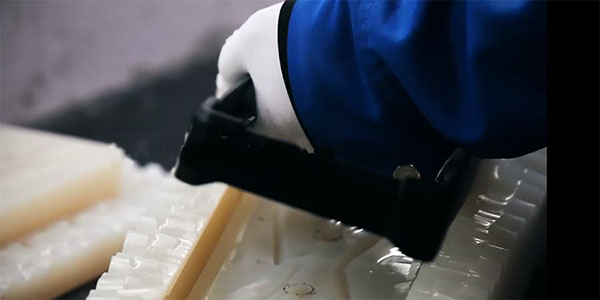
vacuum casting products*
Vacuum Casting Machine
Then, in the vacuum casting machines, there are two mugs (i.e. components) with casting resins and other liquids including a colorful one (if you want your object/product to have color, for instance, you want an orange color tiffin box), then the resin or liquid from one mug is added to the other mug, which already has a liquid (resin or coloring agent) and then it is mixed well. It is mixed under vacuum to release any gases that have been formed in case. Once the mixing process is complete the mold or the liquid is then poured into the silicone casing where there is space i.e. the design created (imprinted) by the master model. Once the liquid is poured into the empty designed space (like how we have designed or shaped vessels for cakes) then it is cast into the oven at 70 degrees Cl. Then, after cooling the silicon casing cover is removed and you get a finished product or material (be it plastic pipes, or plastic mugs, or tiffins, etc.) similar to the original one with which you shaped the silicon casing.
Instances
It is like a carbon copy thing, the only difference is there is a complex process of heating it and cooling it, and then packing it. It is like making different shapes of cake in simple words. For instance, like how you have an aluminum vessel for cake in round, square, and heart shape and how the material is put and heated, similarly, it is with vacuum casing, the difference is that instead of the aluminum vessel (incase of cake) silicon-rubber casing is used.
Reference
*Image from https://www.bolesolutions.com/