Parts manufacturing is a very complex process if you haven’t made up your mind about the material you want to use to create your product. These are the type of decisions that can turn into a nightmare when it comes to logistics. The most popular manufacturing methods out there are die casting and plastic injection molding, but the big question is: which one of them is better? The answer is not as black and white as you may think, so let’s get through with this brief analysis to understand the pros and cons of each one of these means to mas create products.
Die Casting vs. Injection Molding – Common Grounds
Both procedures to craft parts are essentially the same at many stages. The basic motions on both include the creation of a die or a mold shaped after the part you want to create. After the mold passes approval, the product goes into production. In both manufacturing methods, you need to liquefy raw materials and use increased pressure and heat to inject the molten liquid into the die or mold. After that, it needs to cool off using internal lines for the mold or die sprays on the die cavities. After that process is done, it’s time to open the die or mold and remove the product.
The main difference between die casting and injection molding is that die casting uses metal. The most common choice is aluminum alloy, as the primary material. Injection molding uses plastics and polymers. If you are expecting us to tell you bluntly which one is the best, we are sorry, but it’s not as easy as that. The type of manufacturing projects seems to affect a lot the choice of material to create a part. While it’s true that plastic injection molding appears to be overtaking die cast metal parts with every new upgrade done by many companies, there are still many things that plastic can’t handle and only die cast metal gets the job done.
To make things a bit easier, we have compiled a brief list of the benefits you can get with both manufacturing procedures, as well as a brief explanation for each one of them, take a moment to process this information.
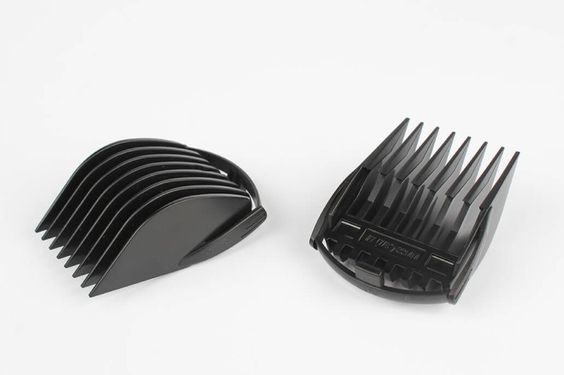
plastic injection molding parts*
Benefits of Working with Plastic Injection Molding
· It’s Faster
You can get production done a lot quicker since the molding process is a lot more flexible and crafting a prototype it’s not as difficult since the same materials can be used to create one for tests
· It’s Versatile
When you work with plastic Injection molds, you can mix as many polymers as you want to get the desired finish on the part you are about to create. Even colors can be added to make the part more unique
· It’s Customizable
The fact that you can use fillers to increase the strength of the polymers you are working with, it’s a highlight and a great advantage. Your product can be as sturdy as you need it to be.
· It’s Reliable
Working with plastic injection molding has proven to be very efficient over the years, the rates of faulty products are meager, and they reach some exceptional levels of accuracy out of the mold.
Benefits of Working with Die Casting Metals
· It’s a One-Shot Operation
Manufacturing parts using die cast metals are not as imprecise as it can happen with plastic injection molding. Molten aluminum reaches every corner of the die, and there is no need for secondary treatments or tryouts.
· It’s Easier to handle the Difficult
You would think that given the malleable nature of plastic casting something with it would be easier, but it’s still a very imprecise process when it comes to filling and wall thickness. Die cast metal does all of this without problems since the metal hardens in place and takes hold until it0s released.
· It’s Durable
This one’s a no brainer. By using die cast metals, we can create high-quality products with far better tolerance that can last much longer. Die cast metals can withstand the tests of time for a very long time.
· It’s Efficient
While it’s true that processing metals take a bit longer than processing plastics, the manufacturing process by itself takes a lot less time than plastic injection molding, and the rate of faulty product is nearly non-existent given the accuracy of the procedure.
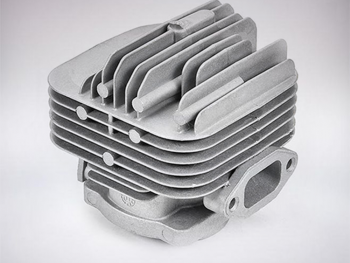
die casting part**
The Final Call
If you are still wondering which manufacturing method you should choose, you need to take a close look at the big picture related to your project. If you need to create a lot of parts at low costs, injection molding is the way to go. But if you require accuracy and fidelity to your design, die casting is the best option for you. It works better to create complex parts in short notice, and it will make them durable and lasting.
Reference
*Image from on http://www.plastopialtd.com
**Image from on http://www.chinastrongd.com