Many times, we see in the market duplicate models or materials of a particular object. Most of the time when people see such they don’t understand how it is made or what is the process involved in the creation of such duplicate material or model. One of the methods that are used in the creation of such duplicate models is the vacuum casting method. But this process of vacuum casting is mainly done on various types of plastic material. I will give you a few more illustrations of vacuum casting– the beautiful colored and different shapes and sizes or similar shapes and sizes the different color plastic mugs, glasses, pipes, balls, caps, etc. that you see are because of vacuum casting. You can also call vacuum casting a process of creating duplicate items or duplication.
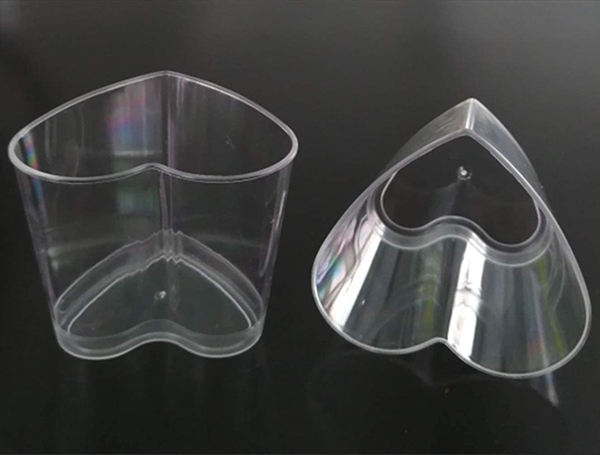
plastic cups*
Process of Vacuum Casting
One of the grotesque things is that if you check online about vacuum casting, then you will not understand a single word on the same because of the use of heavy words like prototype, resin, etc. which a man of common comprehension will not be able to catch fast easily. Let’s look at how vacuum casting is done? In the process of vacuum casting any master model or object of a particular plastic, the product is used. It can be a tiffin box, or a plastic ball or mugs, etc. It is put into a rubber silicon casing for getting the shape imprinted on the casing. To remove any kind of air bubbles the vacuum is applied to the silicon mold. Then, afterward, it is heated in the heater for 40 degrees CL. The heater is like an oven. After the cooling process is completed, the master model is removed and the mold is cut from the casing. Then, in the silicon casing, you will get the perfect model or replication of the object after which the casing is sealed.
Process of Colorful Resins and Liquids Pouring
After a few more steps there are 2 mugs in the vacuum casting machines which are comprised of casting resins and colorful liquids. After you have chosen your color, the resin or liquid from one mug is poured down on the other mug and mixed well with the liquid, which has a coloring agent. Then, it is mixed well under the vacuum and the reasons for mixing well are so that if any gases are formed they should be released. If the gases are not released, then there can be a defect in the product outcome.
Instances of Defect
For instance, when you buy a plastic mug and see some places hard and with a hole like a shape and not exactly a hole but just the shape (extra round shape) in any place around the mug it is because the liquids had gases. Then later the liquid is poured into the silicone casing where there is space for the shape i.e. the designed space and then it is cast into the heater for 70 degrees CL. And once it is cooled off, it is carefully removed and you get the replicated model of the original object.
Reference
*Image from https://www.ubuy.sk/