Manufacturing tasks have evolved to levels that would surprise anyone in this world. This ever-changing industry creates something new to make life easier on the companies and technicians that create products every single day using CNC machines, CNC mills, and 3D prototypes. Most of these companies go at great lengths to be on top of the game. The well-established players are the ones funding research to optimize existing technology and be able to deliver quality parts on time.
CNC milling is a delicate stage in the manufacturing world. These machines are used to trim materials and create new products out of them. The devices used for milling can also be included in complex projects to enhance the features of a product by giving them a cleaner finish. Milling machines are primarily used to create products by removing parts of any given material. These machines are designed to create functional products, so there is very little artistry to explore here.
The Hardships of the Past Vs. The Accommodations of the Present
As is the case with many tasks in the manufacturing world, milling was done following manual procedures. It used to take a lot of time and resources to get heavy materials such as metals and wood milled adequately. In 2019, technological advances allow milling technicians to handle any material with ease. Most modern CNC milling shops work with computer systems to control the devices doing all the work.
There are a few CNC milling features achieved by machines that used to be handled by a man in the past. We share with you some of them and how they work:
· Automated Tool Changer
In the old days, a crafter had to use manual tools to achieve the perfect finish on a milled piece. Even with the first machines, these issues weren’t solved at all. The technician needed to change the cutting tools at different stages of the job. The fact still stands that CNC milling machines require various cutting tools to do what they need to do. With automated tools changers, the CNC milling machine will use the cutting tools equipped on it after being programmed to do so. The only task performed by the technician with this feature in place is feeding the data to the machine.
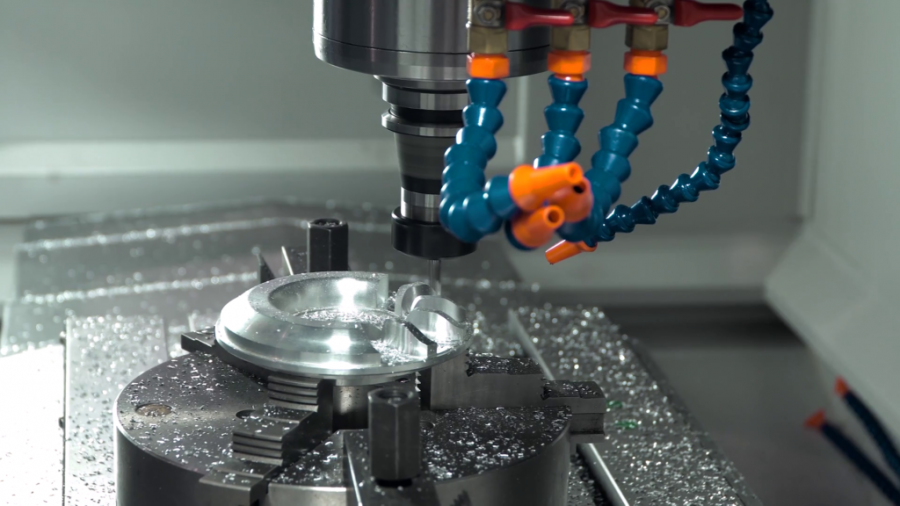
cnc milling services*
· CAD/CAM Software
The reason most manufacturing jobs took a lot of time in the past was that the design stage consumed most of it. With CAD/CAM systems in place, we can use computers to handle all phases of design with a few keystrokes. These systems allow milling shops to control the specs of the part, and they also feed the data to the milling machines. That way, we can get a milling task done in a matter of days without having to waste time.
· Cut-off Functions
The past wasn’t kind to cutting tasks on manufacturing. Working with hard materials required some of the most specialized tools and professionals in the field. It was a bothersome task, and also an expensive one. A modern milling machine can handle any task related to its basic function pretty easily. The greatest feature of this technology is the ability to multitask it based on our needs. CNC milling machines can cut and saw large pieces of raw materials. The cutting-off feature of CNC milling machines is handy to create even-sized products and components.
· Display Units
In the past, manufacturing developers and technicians had to check the specs on paper at every turn. These days, they don’t have to rely on this old-fashioned technique anymore. With display units in place, the technician can check the setting and the specs of the milling machine. They can also use to examine a graphic simulation of the cutting tools to monitor their performance. Display units are pretty helpful to check any information about the milling operation.
· Pallet Changers
Technicians no longer have to work milling tasks on different stages. In the past, these professionals had to create a scheduled plan to make sure the milling was done with precision, using the right tool for every stage. With pallet changers in place, this is no longer a reason for concern. These tools change, removes, and replace all the tools used by the milling machine, making them more efficient and time-saving.
· Rotary Tables
A lot of milling jobs require load and unloads of the plate or sheet that can make the task pretty heavy on the technician. Since many tasks are not done in fixed positions, rotary tables have become a norm in the industry. With this feature in place, technicians can rotate the workpiece to suit the task and achieve a genuine milled part.
All of these features can help to achieve more efficient milling. The latest CNC milling machines are loaded with most of these, especially if they are designed to produce larger amounts of products with quick turnaround times.
Reference
*Image from http://lasvegasmachineandfab.com