Out of all the skills requiring craftsmanship in the manufacturing world, CNC machining is widely used to create custom parts in accordance with required levels of strength as well as different tolerances. It’s one of the most cost-efficiently means to make a prototype work out, and it’s widely acknowledged as one of the best methods to produce parts. Optimizing CNC machining tasks is undoubtedly a great solution that can help manufacturers to accelerate production times and saving money as well. These are some of the best suggestions you should follow:
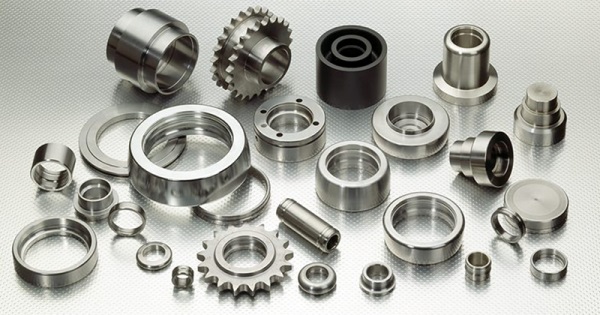
cnc machining parts*
· Round-up Internal Corners on Your Parts
Most CNC machining tools such as mills or cutters always leave rounded-inside corners. These corner radiuses can be reduced using a smaller machining tool, but you will need additional hardware as well to machine away residue material. You will also have to handle more passes at lower speeds to minimize deflection or to avoid breaking the tool. As you can expect, this will add more time to the task, but the finished result will be impeccable.
Among professional technicians, the best suggestions indicate that the correct course of action is to add more inside corner radius on at least one-third of the depth of the cavity. Next, we should use the same radius in every inner edge. As you can imagine, this will help you get rid of any need for tool changes. It will also add complexity to the piece and can increase run time significantly.
· Avoid All Forms of Deep Cavities
The finishing point of mill cutting tools has a very narrow cutting length. They offer their best performance when they have to cut cavities that are three times larger as their diameter. To keep costs low, it would best to limit the depth of the cavity to at least four times the width of the tool. That way, we can get the best results. If you go bigger than this, the costs will go up, and you will need additional specialized tooling such as multi-axis CNC systems. If by any given reason you need larger cavity depth, you will better off using customized parts with variable cavity depths.
· Make Sure to Increase the Thickness of the Walls
A lot of CNC parts are created with fragile walls; these are the ones that break easily. As you can imagine, the second-hand effect is that the whole task slows down a lot. Thin walls also cause a lot of distortion on each part, and the sole effort of machining one becomes a hardship. Thick walls will help you save a lot of time and money. All you have to do is keep the measurements at 0.8mm for metal pieces and 1.5mm for plastic parts.
· Make Sure the Depth of Tapped Holes is Optimized
When you have to deal with tapped holes increasing the length of the thread in the holes does nothing to hold the bolt tighter. You need to rely on the first three turns to get the work done. If you go deeper than that by any reason, you will increase the risk of breaking the tap and make the whole process last longer. To work as they should, any thread needs to hold no more than three times of the hole’s diameter, and that’s it.
· Put a Limit to Tight Tolerances
This is required for the functionality and overall look of very few surfaces. If a CNC machined part has too many tight tolerances, it will be incredibly expensive to be manufactured. The amount of CNC machining that goes into it requires a lot of time to get done right. Is best to use this just when the task really demands it and even so, is best to never go above the standard tolerances of ± 0.125 mm, which is more than enough for most parts.
· Keep Small Features to a Minimum
Small details on any machined part add layers of complexity that you don’t need if you are time- conscious. Do your best to avoid complex features such as micro-holes, they take too much time, and they should be handled only if the task demands it. If it can’t be avoided, do your best to standardize those features to keep costs low.
· Try to Split the Complex Parts
Making some assembly required is going to save you a lot of time and money in the long run. You can make every single complex project simpler by machining simple to be joined later. This is way cheaper than machining a larger, more complex piece. This works pretty well even if your clients have deep pockets and can afford the procedure. Your CNC machines will work better, faster, and maintenance costs will be kept to a minimum. It’s also a great way to prevent any mistakes with retooling or redesigns.
*Image from http://virdiindustries.com