Every single CNC milling operation requires mounting. If you don’t know how to do it, we have a few solutions for you to handle this stage like a pro. The nature of CNC procedures is quite contradictory. On one hand, we have additive manufacturing that uses 3D printing technology to create new products from scratch. On the other hand, we have subtractive manufacturing, such as milling and cutting, that takes apart a workpiece to create something new. Both stances can be benefited from proper holding solutions to get the task at hand done efficiently.
Holding down raw material in place sounds easy at first sight, but it’s actually one of the hardest parts of manufacturing. Sudden movements have caused entire production cycles to be delayed for days. In CNC workshops, most of the solutions devised to keep workpieces from moving are easy to apply due to the design of most machines. The cold hard truth is that some 3D printers and the occasional CNC milling machine lack the proper support to help technicians do their job as they should. That’s when human inventiveness steps forwards and creates a solution.
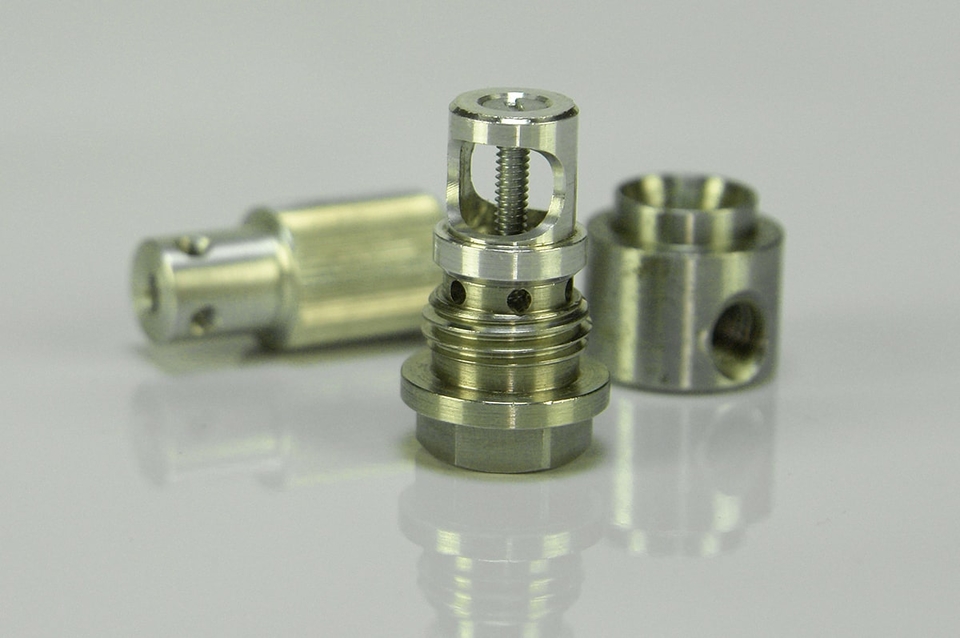
CNC milling parts*
A Full Guide of Holding Solutions for CNC Machining Tasks
In the following lines, we are going to discuss a few holding solutions for CNC machines. Most of the proposals gathered here are proven solutions that were deemed feasible to be placed in this compilation. If you have difficulties with your CNC milling machine or any other piece of equipment of your manufacturing line, feel free to use any of these.
Double-Sided foam tape
This holding solution works really well with sheets of material or with blocks. Double-sided foam tape is probably the oldest trick in the book. It is also considered the best holding material in other industries, such as construction. You only need to place some tape at the bottom of the material and get it in place in the worktable. Your workpiece will be slightly lifted over the table, but it won’t be enough to mess with the calculations of the data placed on the software. Pro-tip: make sure that the table and the workpiece are both clean before using the tape!
The Pros
- It’s an easy solution
- It takes away any vibration
- It won’t collide with the tools
The Cons
- You need to clean the piece after it’s done
- You can only use the tape once
Sheet Clamps
This holding solution is best suited for sheet workpieces or PCB. You will need M4X15 fasteners as well as M4 washer and some M4 nuts. Before getting started with this one, you need to look for the set of sheet clamps included with every single CNC machine. They are included to help you hold materials that are up to 6mm thick. Use one of these clamps to mount one side on the CNC table and use them to slide the material on the machine and the second one to block it. This can be a bit tricky if you are not used to handling the clamps, but a little trial and error never hurt anyone.
The Pros
- It is a two-part solution that blocks raw material in all axes
- You can get them in different types and sizes
Cons
- You need to get used to it
Step Clamps
This holding solution works for sheets of material as well as blocks, you will need M4X16-75 fasteners, but this can vary depending on the type of material you are working with. You will also need M4 nuts and a larger M4 washer. To use these clamps, you only need to place one on top of the material and step underneath the other to make sure you get a balanced surface and enough force as you tighten down the piece. You have to make sure that the tool path doesn’t collide with the clamps. Otherwise, you will end up with a broken cutter during the milling.
The Pros
- It is easy to use to mount high materials
- It won’t take much working space
The Cons
- If you are not careful, you will collide with your cutting tool
Using a Printed Vise
The final holding solution is an ideal fix for sheets of material as well as blocks and PCB, making it the most versatile of the list. You will need M4X20 fasteners with hexagonal sockets as well as M4 square nuts. You can look for the printing specs of manufacturing vises on the internet. The ideal fit has two parallel jaws, one that can move and other that remains still. You will handle the sliding mechanisms using the same principles of a lever and a screw to do everything with it. You will be able to mount everything. Be wary of getting a 3mm screwdriver as well to assemble the vise.
The Pros
- Incredibly versatile
- You can find the CAD model on the internet
- It ensures full stability
The Cons
- There is a preset limit at the dimensions of viable materials
- The vise takes a lot of time to get printed
Reference
*Image from https://www.mmautomatic.com/