In simpler terms for those who are not accustomed to technical terms, vacuum casting is the procedure whereby liquid material is drawn from the mold using a vacuum. The entire process of air entrapment is quite significant, especially where patterns and shapes are involved.
The application of casting of the patterns and shapes is involved when undercuts and intricate details are required. At Lt century, we can also use vacuum casting services when the material used in mold making is reinforced with fibers and wires.
Thermoforming is another commonly referred term of vacuum casting as the procedure involves fast prototyping where preheated plastics are used as sheets. Automated casting machines are used in the pre-heating of the materials until they become soft and pliable.
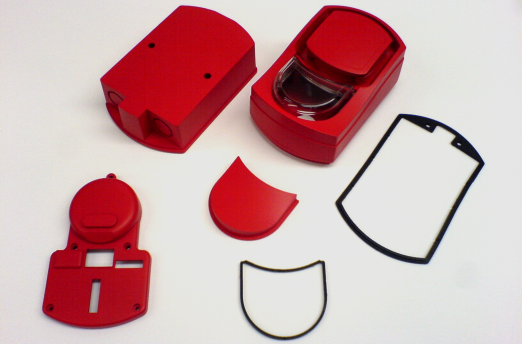
vacuum casting products*
Reasons Why you Should opt for the Vacuum Casting Process
Vacuum casting services produces high-quality products from injection-molded components. The end-product from vacuum casting has an impressive finishing that will incorporate all of your design ideas and objectives that has attracted most of manufacturers and businesses.
At Lt century, we assure you that no other tooling procedure will match the casting that vacuum casting can do.
Application of Vacuum Casting Process
- It’s used to test a part/product before its introduced onto the market
- The process can be used in fast delivery production
- Its used in creating prototypes and models
- It’s used in production for affordable low volume production
- Its used to develop a prototype of any size and shape
How does Vacuum Casting Work?
Master Model
For those who want to use the vacuum casting process, the essential feature that you will need is a high-quality master model. Also, the model should be designed using stereolithography.
It’s essential worth noting that they should use the appropriate appearance and dimensions. So, be rest assured that there will be no flaws or defects that will be transferred onto your model after the vacuum casting process is complete.
The Curing Phases
This phase entails the positioning of the model into a two-part silicone rubber mold. The mold is, in turn, exposed to high temperatures, which ensured that the two parts stick well, so there are no spaces or crevices.
The main aim of the curing process is to fortify the patterns and enhance its durability. After curing, the mold is cut open, exposing a hollow part located at the center, which is the same size as the master model.
The pattern is placed into the vacuum chamber; the material is added into the mold creating the product.
Filling Resins
The mold is filled using an assigned material; the resin is used to copy the traits of industrial materials. To enhance its appearance the coloring pigment or metallic material is added onto the resin material giving it an aesthetic feel
The mold is filled with the resin material, and its inserted onto the vacuum chamber, which ensures no air or bubbles are making sure that the end-product of the vacuum casting process is not damaged.
Reference
*Image from https://www.pdmodels.co.uk/