Choosing the right material is one of the critical aspects of the plastic injection molding process. The materials you will be using will have a direct effect on how the molding process will work and on the performance of the completed part.
When you are choosing a material like plastic, the first thing you should consider is the function of the part and its use. Then, you also have to think about the strength, flexibility, durability, color, and, of course, the cost. To help you understand the injection molding process, here are the most common materials used in the process and its applications.
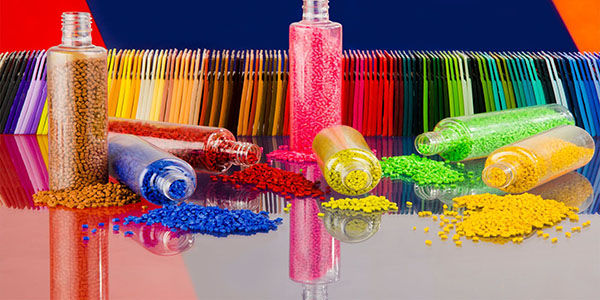
Injection molding materials*
1. Nylon
Nylon or polyamide is used to produce sturdy mechanical parts, including gears, bushing, and bearings in automotive parts. This material is tough, good chemical, and wear resistance and has a high melting temperature.
2. Acrylic
Acrylic is a common material that we find in transparent parts like lighting equipment, windows, and transparent walls. It is often used as an alternative to glass as it possesses high tensile strength and scratch and weather resistant. Acrylic has other unique properties like being tasteless, odorless, and BPA free, hence you will find them used in refrigerators and food containers.
3. Polycarbonate
This material has unique properties and is durable. When used in injection molding, this material has predictable and uniform mold shrinkage. It is often used as a substitute for acrylic when the parts demand more durability. It is not suitable for use with food because it contains BPA.
4. Polyoxymethylene (POM)
This acetal resin is used in manufacturing automotive and mechanical parts that are made from metal. It is referred to as an engineering thermoplastic as it is very tough, rigid, and strong. The most common uses are as fasteners, ball bearings, knife handles, and gears. It has a high resistance to solvents like gasoline and alcohol but not to nitric acid and hydrochloric acid.
5. Polystyrene
In injection molding, there are two types of polystyrene: High Impact Polystyrene (HIPS) and General Purpose Polystyrene (GPPS). It is used for hard cases like toolboxes and housings for power tools. This material is inexpensive but not environmentally friendly.
6. Acrylonitrile Butadiene Styrene (ABS)
This material is described as an engineering grade plastic and opaque thermoplastic polymer. It has many great qualities like toughness, scratch and high impact resistance, and dimensional stability. It is also cheap and has a low melting temperature. Its most common applications are wall socket cover, keyboard keys, and phone adaptors.
7. Polypropylene (PP)
This is most commonly used in the packaging and food storage industry as it never allows chemicals to mix with food products. You can also wash any product made from this material in hot water and have moisture and chemical resistance.
8. Polyethylene (PE)
It is a material that has elasticity, high chemical resistance, electrical insulating properties. Although it is not as hard as other materials, it has a wide variety of applications including milk bottles, trash cans, and plastic bags. It is also the most common injection molding material for producing children’s toys.
9. Thermoplastic Polyurethane (PU)
This material is known for its great tear and tensile strength and elasticity. It is often used in producing parts that need elasticity like rubber and thus, you will find its use in power tools, cable insulations, and items used in sports.
10. Thermoplastic Rubber (TPR)
It is a material that is a combination of rubber and plastic and very convenient to use in injection molding. Since it is made with two materials, it exhibits both properties in addition to excellent weather and chemical resistance. It is used in medical catheters, headphone cables, and suspension bushings.
There you have it, a brief overview of the most common materials used in injection molding, their properties, and applications. You can choose a suitable material based on your unique project needs.
Reference
*Image from https://www.infomediayellowpages.com/