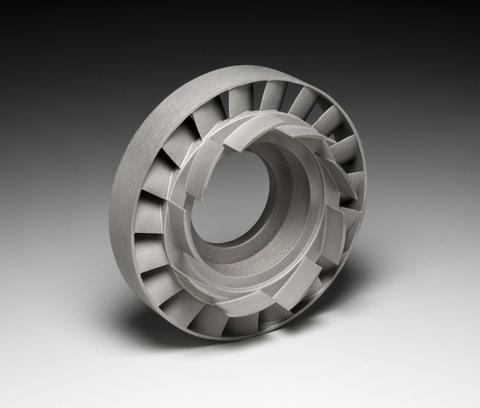
superalloy vacuum casting for generators*
Vacuum casting remains a procedure of removing liquid content into the molding structure. When the molding structure has an air entrapment problem, this may serve as one of the best ways to resolve it. Even if the molding structure has undercuts & hard complications, vacuuming can also help. If the fabric is not allowing the mold to reinforce or become fiber, it’s better to apply a vacuum.
In another way, thermoforming is the name of calling the process above. It’s a procedure that makes the production to occur as a fast prototype. It also makes plastic sheets to be in the preheat state. Materials get automatic preheating conditions in a vacuum machine until they become pliable. While the procedure may be slower, but it makes it possible to avoid casting faults.
Why Engage In Vacuum Casting?
- Quality parts and products are what you get for engaging in this process. The process often has effects on the quality of parts and end products. Most products that pass through this procedure end up displaying a high quality.
- Fast and quick production is another benefit of engaging in the above process. The manufacturing of parts and products will bring large outputs. When talking about time, the casting process remains the best to make you enjoy other tasks. It’s less time-consuming, which means that you have time to do other jobs.
- Another thing that you enjoy is the less expensive cost you spend. It’s cheap, reliable, and affordable.
- Accuracy is one advantage you cannot miss out on when using this process. Products pass through the manufacturing phase and product better quality and result.
- It is adaptable. Irrespective of the materials you use, expect to get flexible and adaptable results.
The Ideal Operation Of A Vacuuming Machine:
The process of operating a vacuum machine can take different methods. From the production stage to the end product, you can expect to follow several steps. The creation of the three-dimensional model is the first step to follow. In this step, users will need to have a top-notch master model.
Step two may involve the curing procedure. The original structure will get a covering from two different rubber synthetic molding containers. The third step involves the resin vacuum casting chamber. At this juncture, you’ll have to fill the molding structure.
Applications For Vacuum Cast Molding:
Household products such as tins, bottles, and plastics.
Drinks and food, either commercial, hobby, or domestic applications.
Industrial and commercial products.
What Is The Future Of The Vacuum Cast Process?
With every application of the process, it’s evident that the world gains a lot. People have been benefiting from the creation of new products and parts. It makes the production of products faster, better, and efficient. One of the most helpful things about the process is that it remains affordable.
People don’t need tons of dollars to start engaging in this process. Apart from affordability, benefiting on its applications remain possible today. Whether it’s health, business, style of life, or building, the process still works. It’s a recommendation from experts for people to start engaging in the process big time.
Reference
*Image from https://chips.en.taiwantrade.com/