It is a versatile and cost-effective, making it useful in many sectors. Automotive, aerospace, and medical device manufacturers utilise it to build moulds for casting complex geometries using a vacuum. This article discusses vacuum casting, its benefits, and its uses in many sectors. This article will explain vacuum casting and why manufacturers worldwide use it.
Introduction
It outperforms conventional manufacturing methods. It can make complex-geometry parts with excellent accuracy and precision. For low-volume production runs, it is cheaper than injection moulding. It is useful for companies that need speedy output. These benefits make vacuum casting a good choice for experimentation and small-scale manufacturing in many sectors.
Process
Moulds are made from master patterns for it. The master pattern might be produced from plastic, metal, or wax. A silicone rubber mould is made around the master pattern in a casting chamber. A vacuum chamber removes air pockets from the silicone rubber mould.
Casting material is put into a mould without air spaces. Vacuum, silicone, or epoxy can be poured or injected into the mould for casting. After pouring the casting material into the mould, it cures for a certain time, depending on the material.
After curing, the mould and part are removed from the vacuum chamber. The part is cleaned, finished, and inspected to satisfy standards.
Advantages
It outperforms other production methods. Its benefits:
- It is perfect for sectors that need complex geometries because of its high accuracy and precision.
- It is cheaper than injection moulding.
- Speedy Turnaround Time: It is perfect for sectors that need speedy output.
- Low-Volume Production: It is perfect for prototyping and small-scale production.
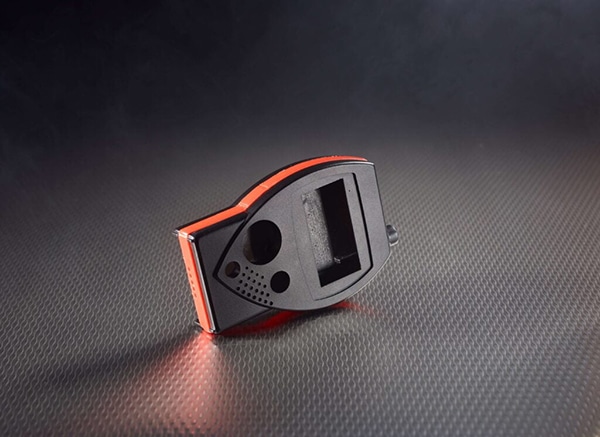
vacuum casting parts*
Applications
Many businesses use it. It is commonly used for:
- Car sector: Small to medium-sized engine covers, dashboard components and interior trim pieces are vacuum cast in the car sector.
- Ducting, brackets and housings are vacuum cast in the aircraft sector.
- Medical Device Industry: It makes prostheses, orthotics, and surgical tools.
- Consumer Goods Industry: It makes toys, electronics and household appliances.
Future of Vacuum Casting
- Integration with Industry 4.0
- Increased Use of Automation
- Advancements in Material Science
Industry 4.0 technology like IoT sensors, AI, and big data analytics will make hoover casting more efficient and cost-effective. Automation may also reduce manual labour, lowering production costs and time. Finally, advances in material science may enable the development of novel its materials, broadening its applicability.
Conclusion
Finally, it has revolutionised the manufacture of complex geometries. It is cost-effective and precise, making it appropriate for many sectors. Automotive, aerospace, medical, and consumer products use it.
In sectors that need complicated geometries, vacuum casting accuracy and precision are crucial. For low-volume production runs, the procedure is cost-effective. It is useful for companies that need speedy output.
Manufacturers are anticipated to use it increasingly as technology improves. Vacuum casting will remain significant in manufacturing for years to come due to its various benefits and uses.
It is a cost-effective, adaptable, and efficient approach to make complicated geometries.
Reference
*Image from https://vacuumcastingsz.com/