The technology and techniques used to create parts and products over the last 20-30 years have significantly changed, computer systems have been incorporated into the manufacturing process making the whole process precise and accurate.
For any company or firm wishing to be successful, prototype molds, CNC machining, and injection molding should be incorporated into their manufacturing techniques to stay competitive in the ever-increasing demanding fields.
Creating mechanical parts and products is not an easy and straightforward process, even with all the automation and improvements in the production sector, the sector is riddled with plenty of challenges especially with regards to design flaws. In this post, we are going to highlight ways of solving these challenges.
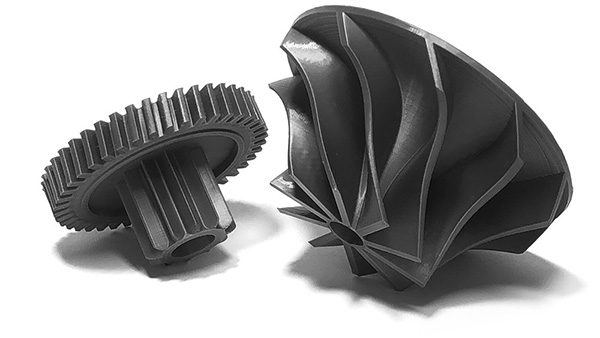
3D printed compressors and gears*
Issues dealing with troubleshooting
Troubleshooting is a key feature of the rapid tooling process, this phase is the most stressful and time-consuming. As a manufacturer, you need to run a lot of tests and experimentation to point out any performance or functionality issues so it can be addressed as soon as possible.
This is the only stage of the manufacturing process that cannot be rushed or scheduled. If the issues arising can be traced back to the design stage, this will present a significant challenge as there will be loss of resources as well as money which might make the entire rapid tooling project a loss-making venture.
Producing a prototype mold will solve all these problems allowing engineers and designers to have smooth and seamless product development. The tooling process can also utilize 3D designer technology that will provide a lot of information and insights on a particular product making it more functional as well as appealing.
The cause production issues
The source of all the manufacturing issues begins from outsourcing, as a client if you outsource your project to a different firm. Plenty of information can get lost in between, it’s always recommended to stick with one firm making the whole process as painless as possible.
Provide all the specs and information to the contracted firm, ensure all your production needs and requirements are met. Be in constant communication with the design and production team which ensures what was conceived during the design phase will have all the specs and measurements.
Dealing with performance-related issues
Given the current trends in the manufacturing world, you need to stay ahead of the curve to stay competitive. A lot of performance-related issues stem back from the initial design phase, work with a firm that cast out/produce a prototype mold using efficient and effective rapid tooling techniques.
The chances of having any transition problems will be minimal, another huge plus of going with a specialized firm is you’ll have on-site professionals that have the necessary skills and techniques to make your project a huge success.
A manufacturing firm that is capable of handling the design phase and development with ease will have little or no problem with handling all the technical equipment that will run the whole manufacturing process in just one cycle. This will significantly reduce the troubleshooting phase saving you a lot of money and time for your project.
Reference
*Image from https://3delft.nl/