Casting is the major manufacturing process which is mostly used in heavy industries. Most of the components like outer casing turbines, lathe bed, valve casing, and hydro turbine blades are manufactured by this means. Major machinery parts are manufactured by the casting process alone because of their accuracy and effectiveness. Different materials can be cast in different shapes easily using the casting process.
Wide varieties of similar casting processes are available as well, below mentioned are some of them
- Sand Casting
- Investment Casting
- Wax Casting
- Die casting
- Centrifugal casting
- Foam Casting
- Vacuum Casting
Several highly trained professional casting equipment is available online, one can choose the one best suitable for their requirements by surfing the internet.
Vacuum casting is better known as urethane casting in the manufacturing world. The process of producing a limited number of high-quality, coloured, textured functional plastic parts. Such physical parts are mainly used for design validation, form fits, market fits and also for some market tests while introducing a product. Among several advanced techniques and 3d printing facilities available, this type of vacuum casting is considered the cost-effective one for manufacturing needs.
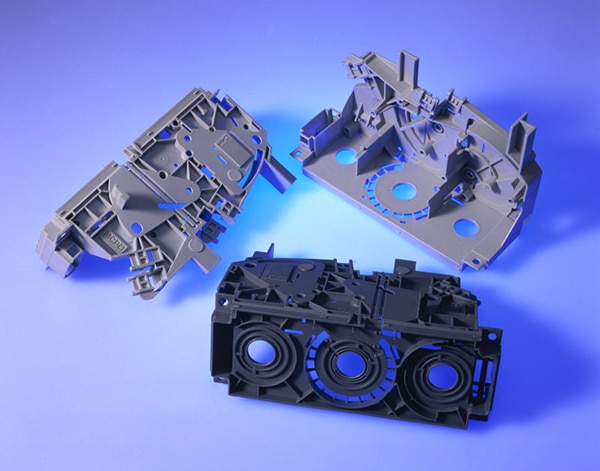
vacuum casting parts*
Step by step process involved in the vacuum casting process is as follows:
- 3D Model – Starts with translating a CAD design into a physical master model that is usually 3D printed and CNC Machined
- Master Pattern Creation – The Master module is then painted with textures as per the manufacturer’s requirements.
- Making rubber Mould – Liquid silicone is poured around the model which is suspended in a box for creating a rubber mould.
- Casting – Mould is then inserted into the oven and precisely cut along the predetermined plane. Different types of casting materials are used based on their natural physical properties like elasticity, rigidity, etc.
- Leaving behind the core and cavity master module is carefully removed from the mould polyurethane resin is poured into the master pattern. Colouring pigments is added to the resin based on the requirements.
- De-molding – Based on our requirement’s pigmented materials are poured into the empty cavity under a vacuum. Modules out of the materials are ready to use and are subjected to quality checks.
Advantages of vacuum casting process:
- High-Quality Finishing
- High accuracy
- Prices and deadlines
Below mentioned are some of the ideal applications of vacuum casting,
- Production of plastic parts
- Production of Equipment’s & Medical Devices
- Automotive parts
- Testing parts Integration
- Ornaments
- Product Marketing
- Food and beverages Industries
- Household products
For instance: The jewellery casting process is a process where you can make customised jewellery as per your requirements at an affordable rate. By using this type of vacuum casting process one can make more jewels easily at a reasonable price. By melting metals and pouring them into the desired shape it can be made possible. By eliminating air bubbles we can give more accurate shapes.
Reference
*Image from https://www.scott-am.com/